2024 key performance highlights:
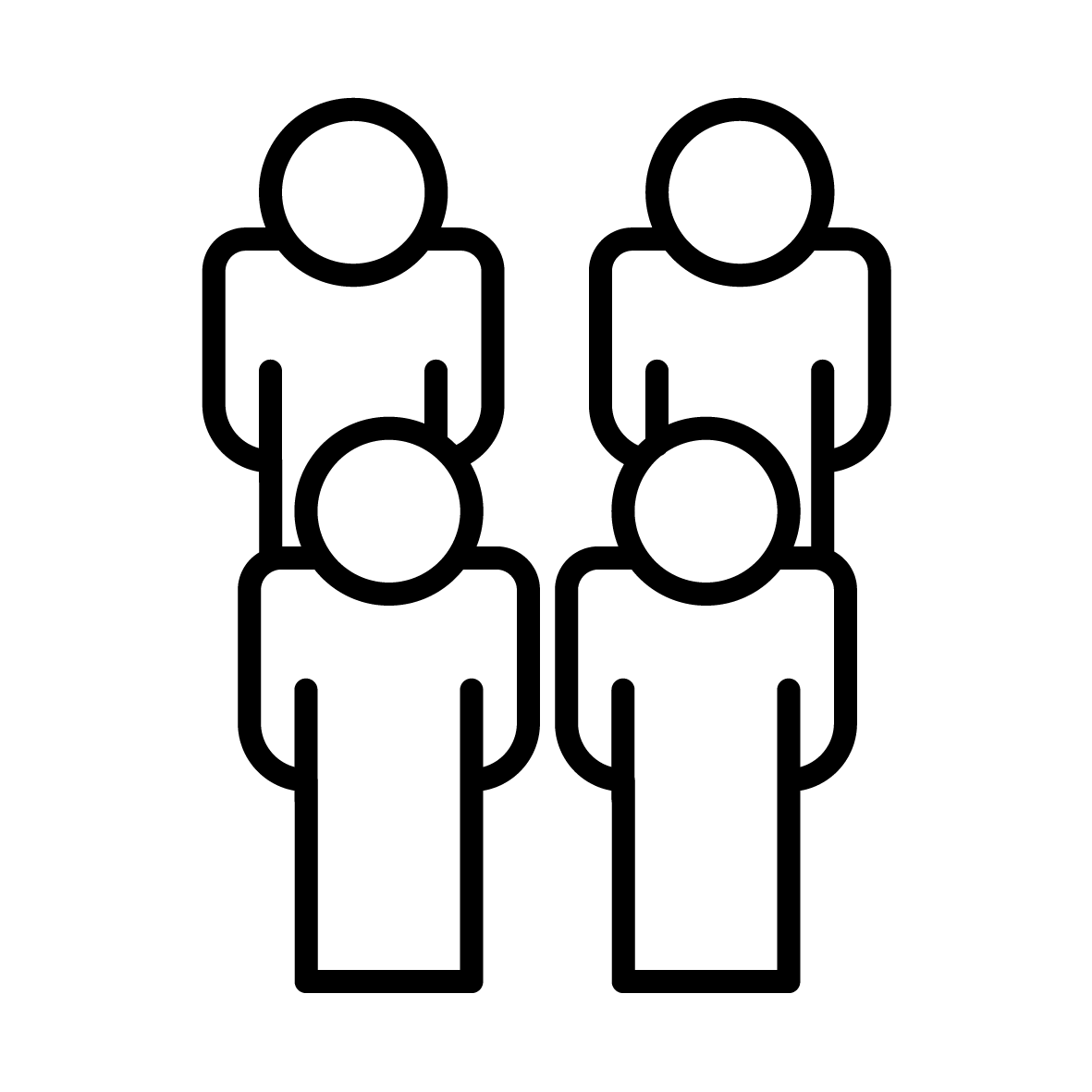
4% decrease
in total employee and contractor accidents
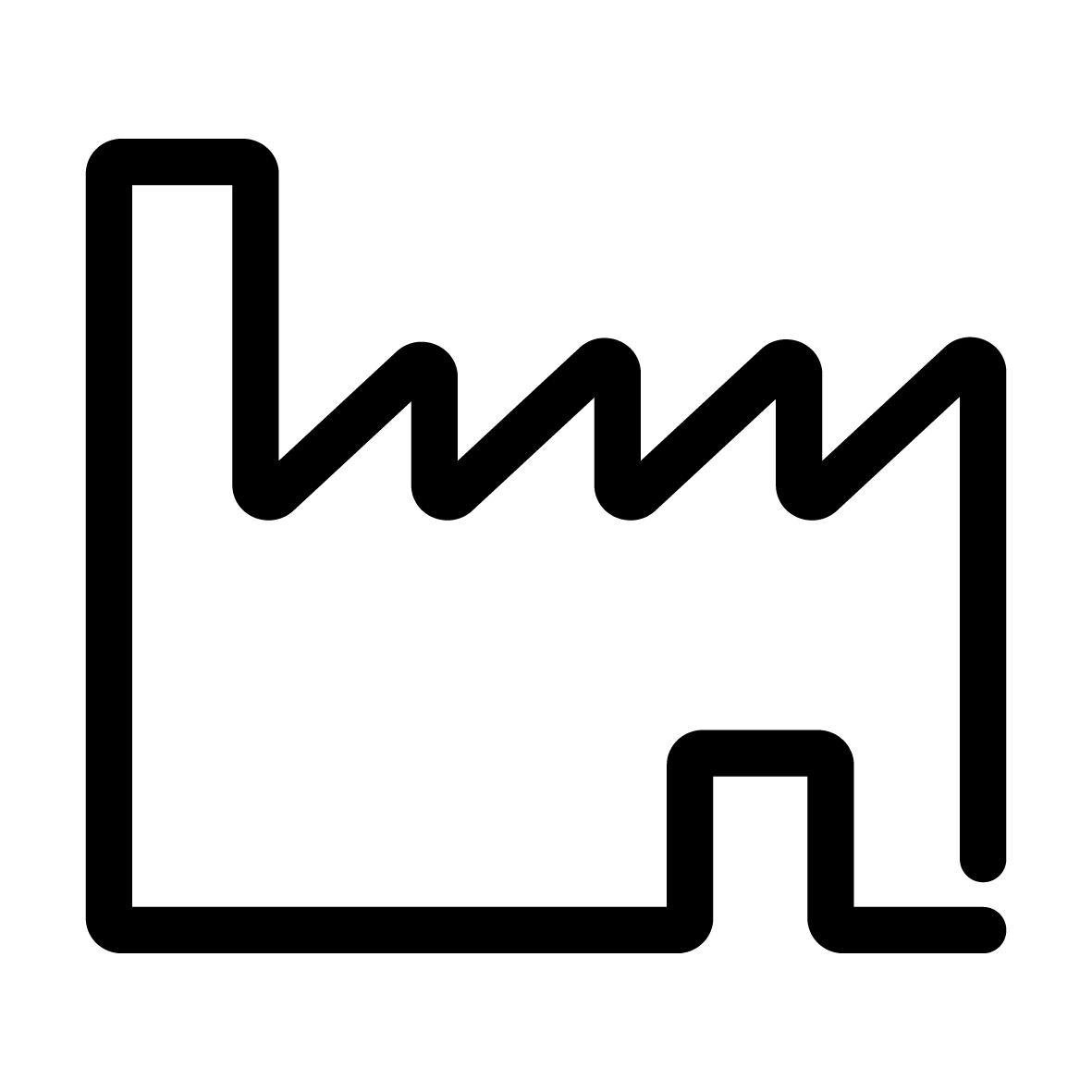
26% reduction
in LOC events
Loss of Containment (LOC) events
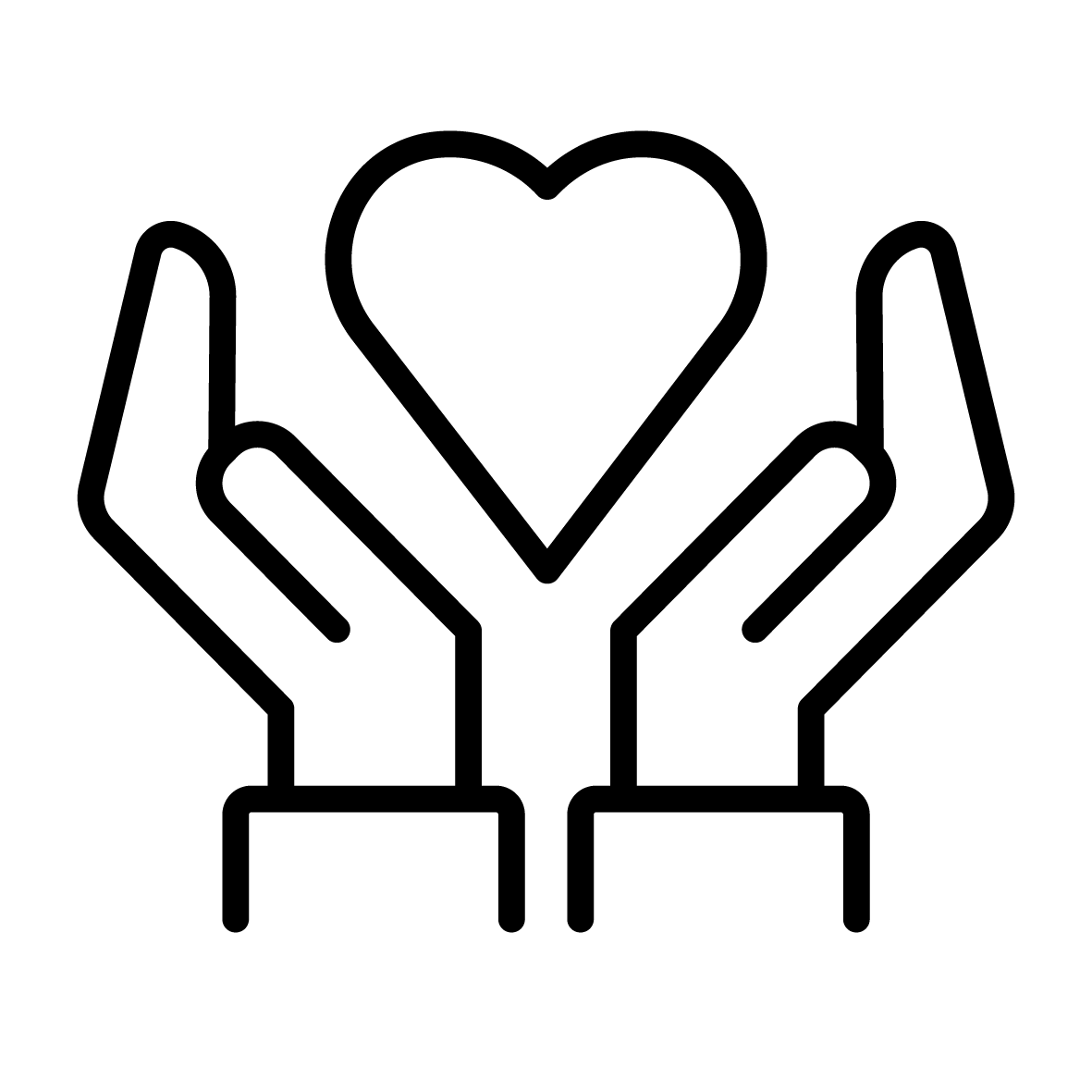
UK CIA health metrics
92% of sites achieved ‘Best Practice’
8% attained ‘Advanced’ ratings in specific areas
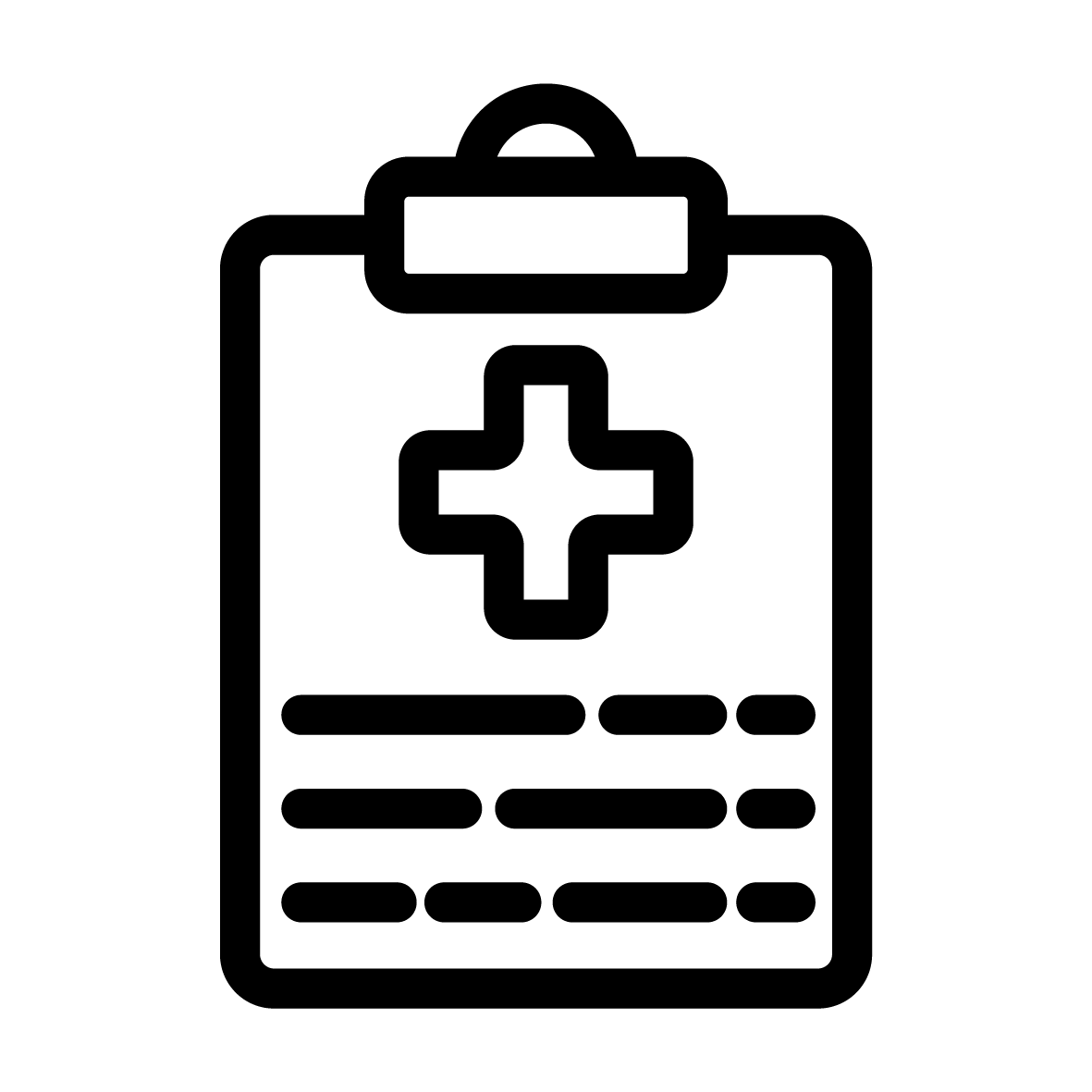
2% increase
in near miss reporting*
*Defined as a learning event that did not cause harm but had the potential to cause injury or loss. The more near misses reported and addressed, the lower the risk of a future accident or incident.
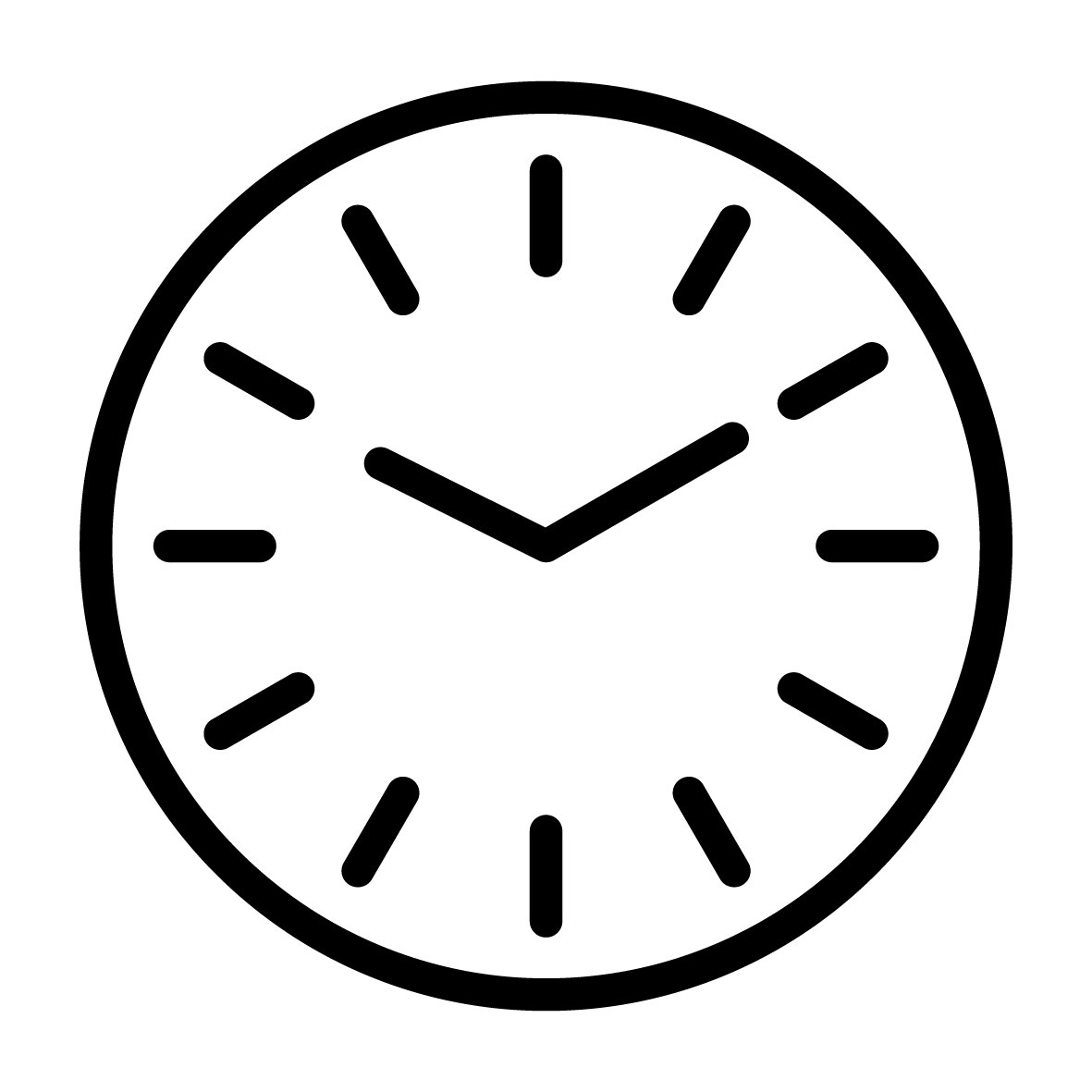
24% reduction
in employee accident rate
per 100,000 hours
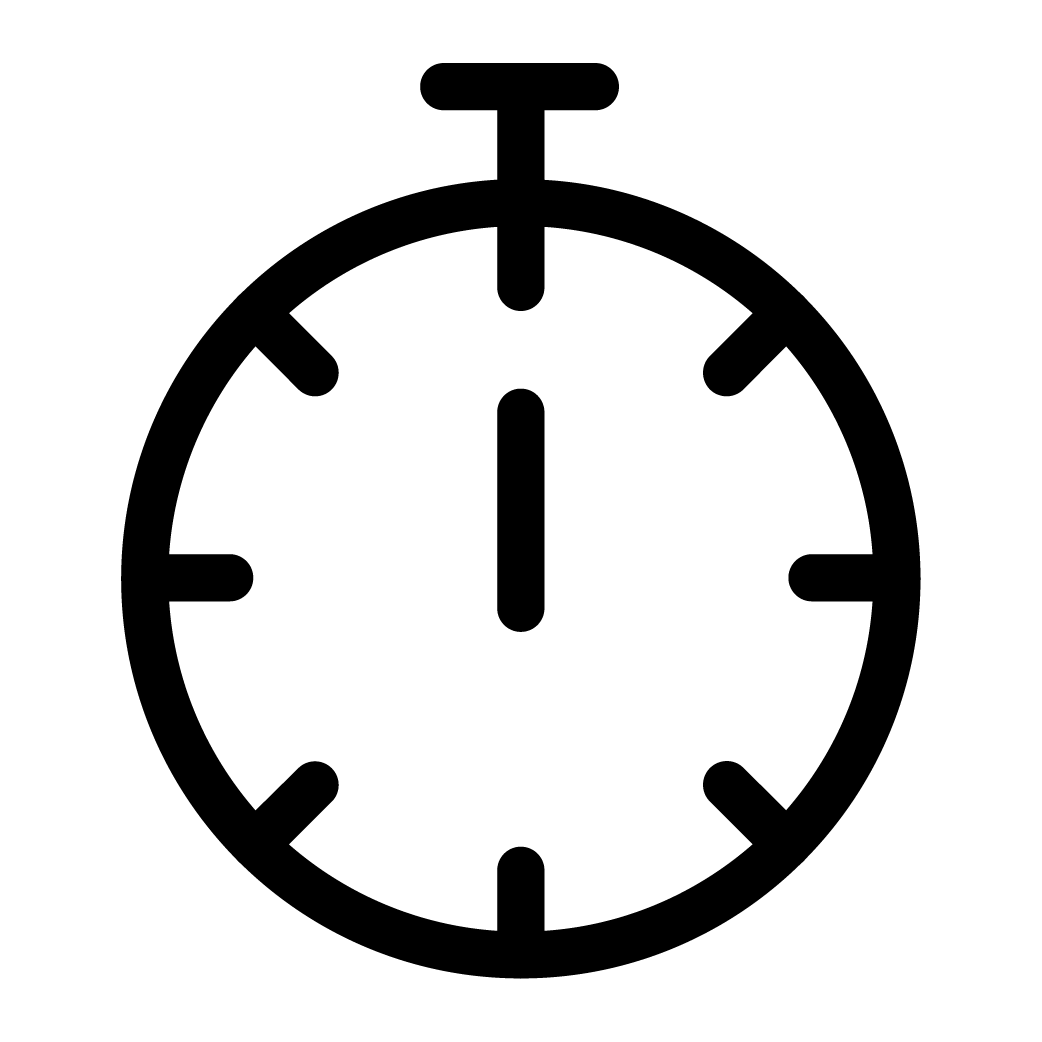
147,769
60-second checks completed
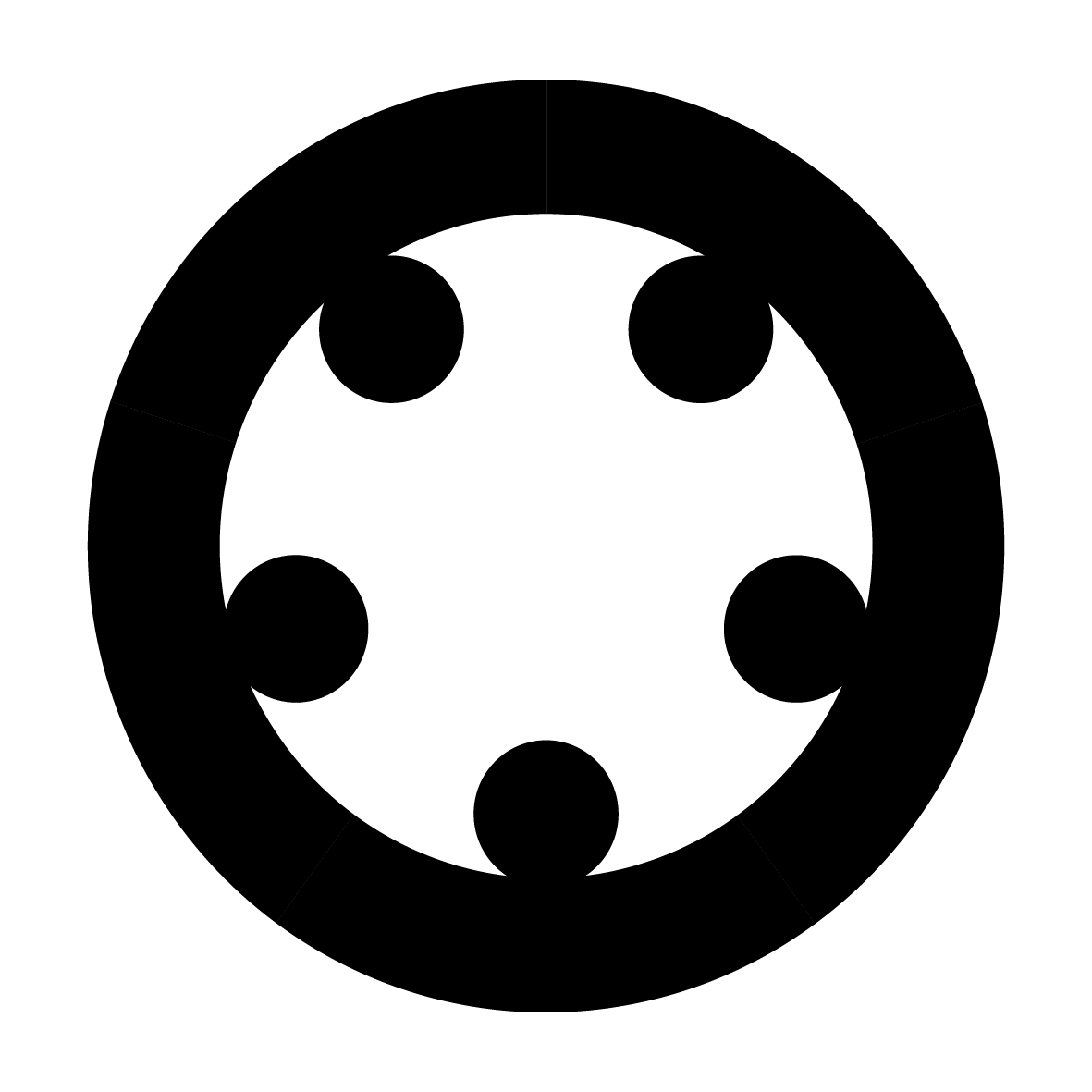
Journey To Zero Harm
12,570 safety interactions completed by employees globally
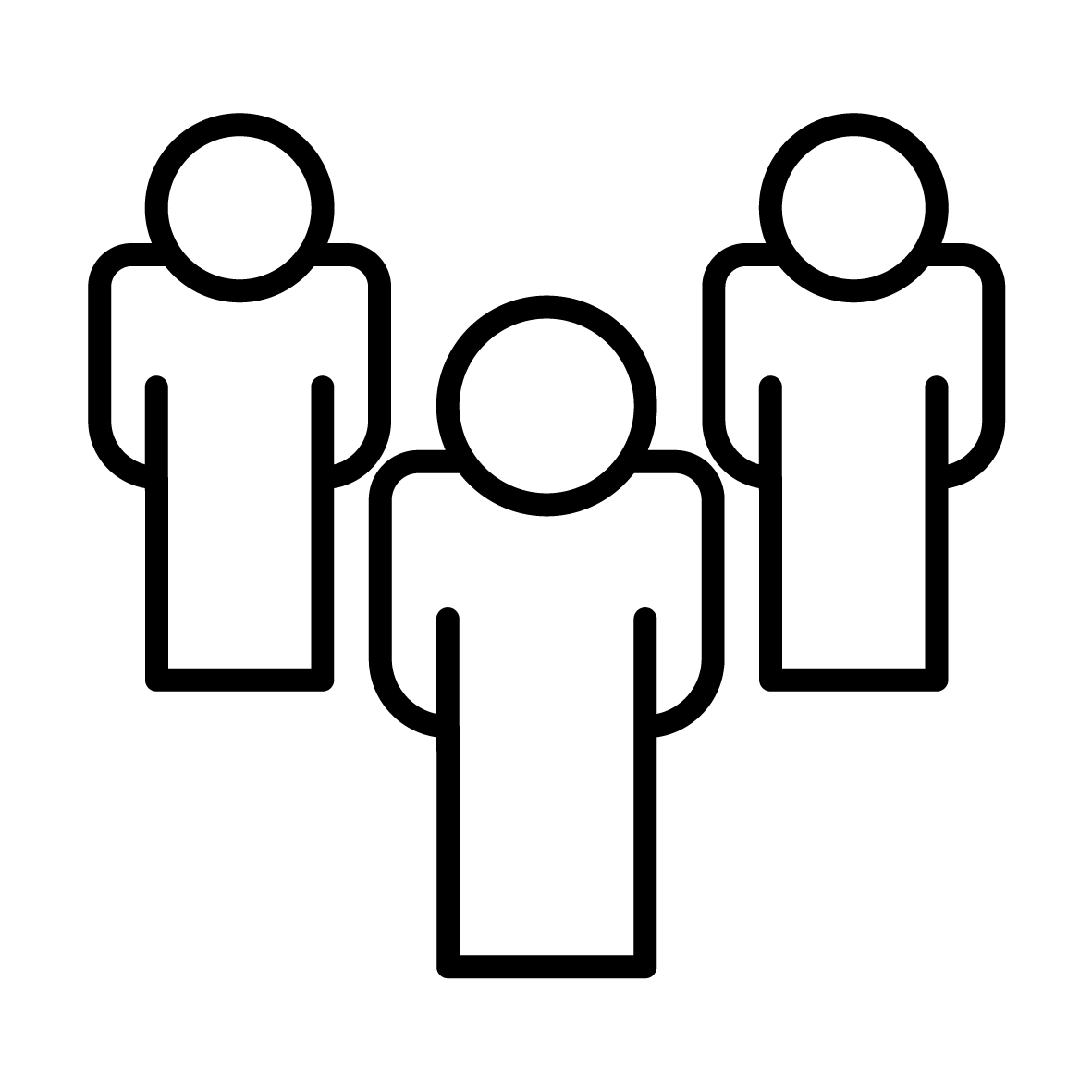
2% decrease
in total accidents recorded
Our SHE Standards and Policy
We set high standards for process and occupational safety, which is managed by our network of Safety, Health and Environment (SHE) professionals, who are responsible for maintaining high standards and implementing our SHE Policy.
SHE Objectives
We follow three core objectives:
⢠No one gets hurt
⢠We do not negatively impact our neighbours
⢠We aim to minimize our impact on the environment
SHE Leadership
Our RESPECT Committee oversees our global SHE policies, sets objectives, and monitors ongoing performance. The committee, led by our CEO, Patrick S. Williams, includes members of the Senior Leadership team and reports directly to our Board of Directors.
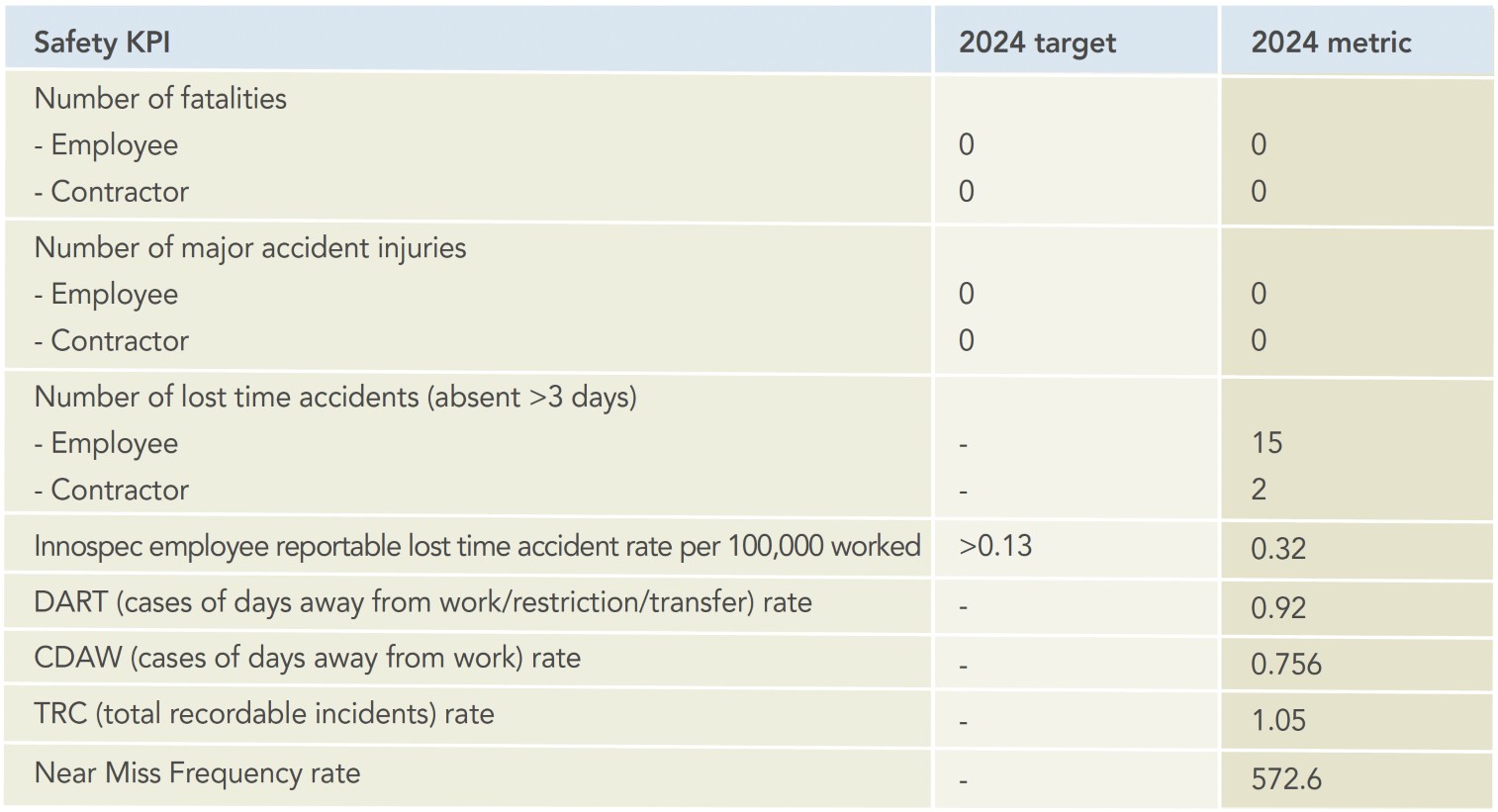
2024 safety performance
Each year we set a group safety objective and target of achieving zero fatalities or major work-related injury accidents to employees or third parties. We are pleased to report that in 2024 we met this target.
We also set a group safety target of achieving a zero Innospec employee reportable lost time accident (IRLTA) frequency rate. As a minimum acceptable standard, we expect to perform better than the industry average for the UK chemical sector. Unfortunately, in 2024 there were fifteen employee IRLTAs. Each accident has been investigated and measures put in place to prevent similar accidents from happening in the future. The learnings from these events have been shared across all sites. As a result of these accidents our IRLTA frequency rate for the period was 0.32 per 100,000 hours, higher than in previous years.
External Recognition
Cigna Healthy Workforce Designation
In 2024, our US teams received their third consecutive Cigna Healthy Workforce Designation⢠Gold Level Award. This recognizes that senior leadership offers extensive support for employee well-being programs through organizational commitment. This includes programs and resources that support various dimensions of well-being in addition to health equity considerations that creates a supportive culture, and safe, healthy workspace.
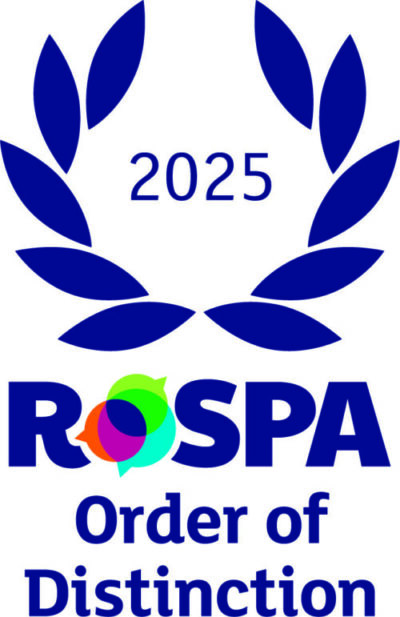
The Royal Society for the Prevention of Accidents (RoSPA)
Our Ellesmere Port, UK site received its eighth Order of Distinction Award from the Royal Society for the Prevention of Accidents (RoSPA) for their excellent safety performance in 2024. The award acknowledges 23 consecutive years of achieving RoSPA Gold.
Internal Recognition
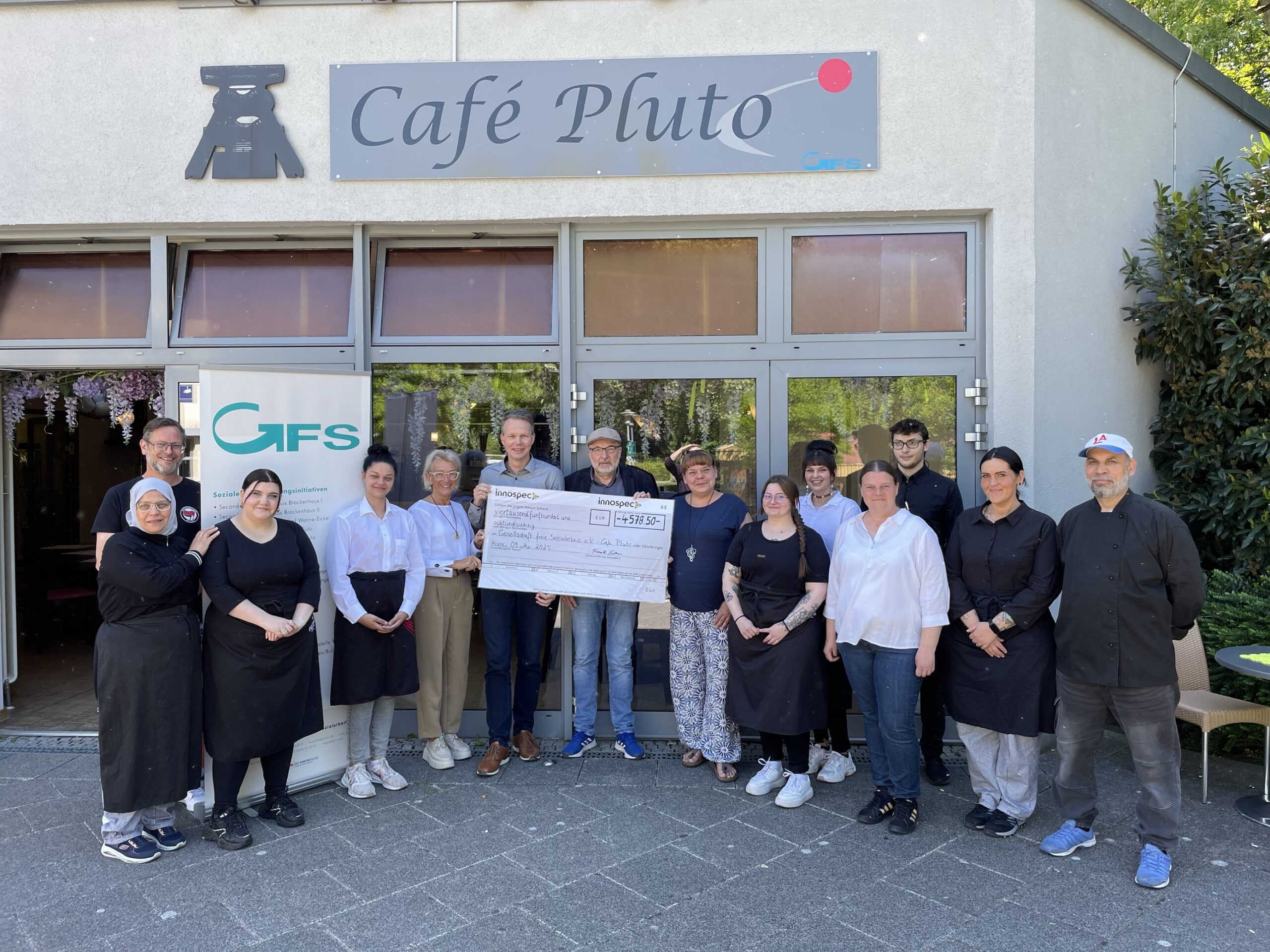
2024 corporate safety awards:
Gold award (US$5,000 donation to charity)
- 11 years without IRLTA: Herne (Germany)
- 9 years without IRLTA: Oklahoma, TX (US)
- 5 years without IRLTA: Chemsil, LA (US)
- 5 years without IRLTA: Midland, TX (US)
Bronze award (US$1,000 donation to charity)
- 1 year without IRLTA: Salisbury, NC (US)
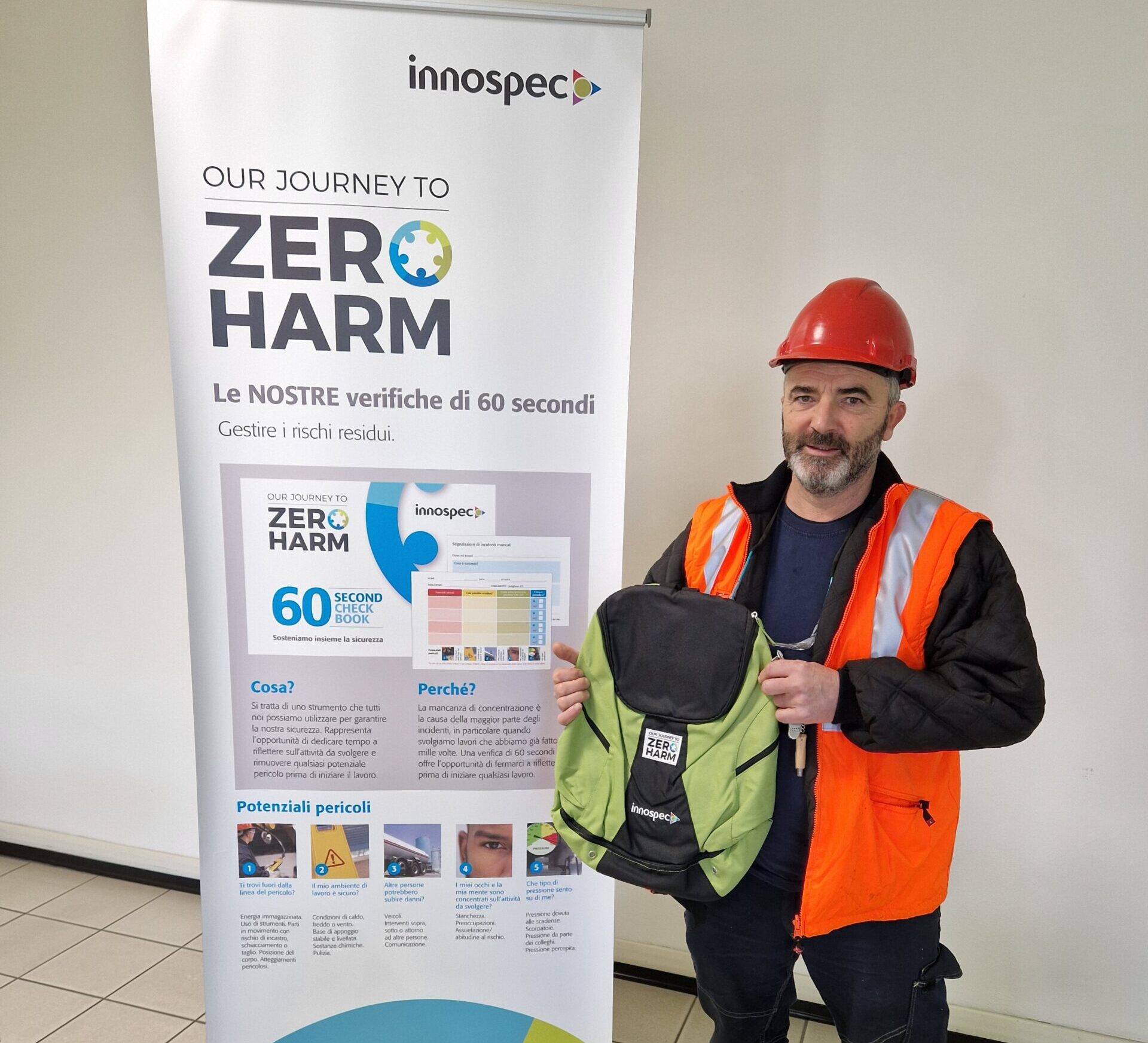
2024 corporate safety certificates:
Gold certificate:
- 2 million employee-hours worked: Midland, TX (US)
- 1 million employee-hours worked: Castiglione (Italy)
Silver certificate:
- ½ million employee-hours worked: St Mihiel (France)
Explore more about health, safety & well-being at Innospec
Process Safety
We have worked diligently to develop and implement a robust process safety management system that controls our process hazards and minimizes the risk of process safety incidents.
Learn MoreOccupational Safety
We focus on understanding how the behaviour of individuals contributes to safety culture. Integrating years of experience, investigations and advice from external safety experts, enables us to have everything in place to provide the safest possible working environment.
Learn MoreJourney To Zero Harm
Our company-wide Journey To Zero Harm (JTZH) program is our key strategic tool to help reduce accident numbers by encouraging everyone to take responsibility for carrying out a personal safety risk assessment before starting an activity.
Learn MoreHealth and Well-being
Looking after the well-being of our employees is key to the success of our business. By providing ongoing support we can ensure we make the most of a personās experience, dedication and creative skills at work.
Learn More