*Innospec do not directly disturb land or generate tailing waste.
- Total Waste
- Waste Handling Routes
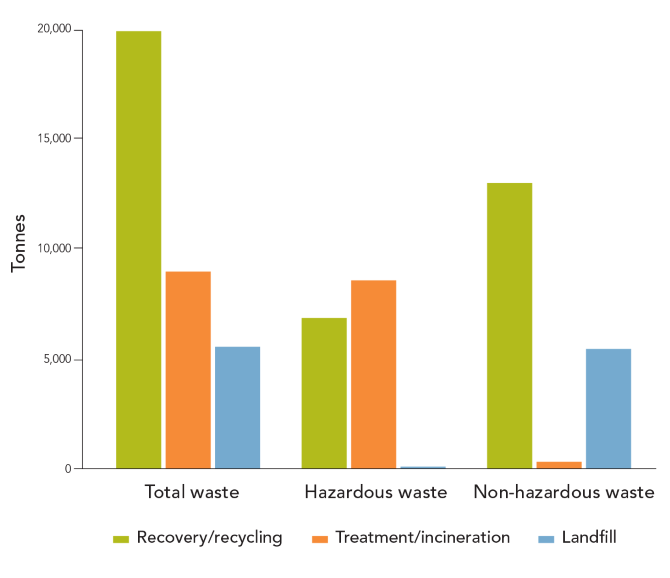
Waste data reported includes routine production waste in addition to ad hoc removal of aging stock, construction and demolition waste streams. As such reported data varies year to year. In 2023, several sites completed one-off construction projects and removal of aging stock programs that did not take place in 2024. Switching some Oilfield Services customers to bulk deliveries in 2024 reduced the use of totes and the subsequent need to recover returned totes. This reduction in waste was partially offset by waste generated as a result of increased production to meet customer demand.
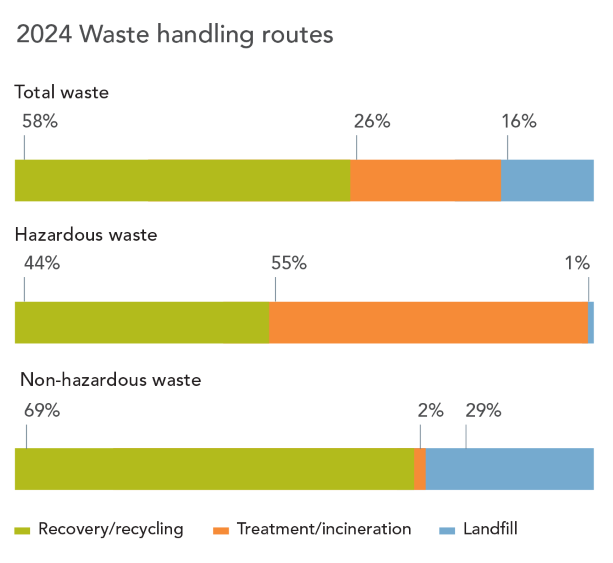
Reducing Our Waste
We have introduced a number of initiatives to reduce waste across our sites and prioritize recovery and reuse, with the aim of contributing to the development of a circular economy. Activities in 2024 include:
Leuna, Germany
Our site in Leuna is demonstrating how circularity principles can be effectively integrated into daily operations. By participating in a European pallet return scheme, Leuna has attained a recovery rate of over 65%, calculated by the percentage of pallets returned to PRS compared to the number of pallets received. This accomplishment has earned them the PRS Green Label certification, placing them among the top 30% of companies involved in the scheme. Since they started in the program in 2021, they have returned 782 pallets.
Midland / Pleasanton, US
These sites now use a third-party company to collect and recycle alkaline (AA, AAA, etc.) batteries that were previously thrown away. These batteries may otherwise leak hazardous materials into landfill sites and eventually groundwater if not properly disposed of or recycled.
Castiglione, Italy
To reduce wastage caused by the periodic sampling of a production process and drainage of tank lines, the site has implemented a new product recovery system. The collected material is tested and then recovered into the next production batch of the product. This is avoiding 12 tonnes of product from being sent for waste treatment each year and also reduces raw material usage.
Salisbury, US
The site has upgraded the device that removes pollutants from our industrial exhaust stream, avoiding the generation of Hydrochloric Acid, a hazardous waste material. This new equipment for our existing process will save 270,000 pounds of hazardous waste every year.
Midland / Pleasanton, US
The sites are returning oil and water samples from our analytical labs back to customers once testing is complete, preventing it from being sent to landfill and benefiting the customer.