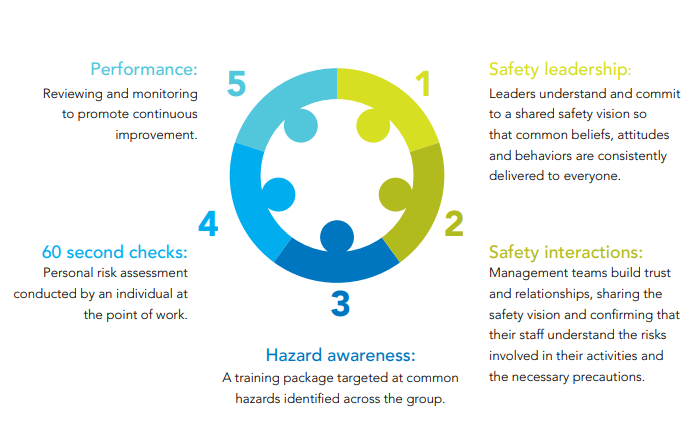
JTZH strategy
The global rollout of the program to all employees ensures Board and leadership buy-in, demonstrating that the behavior expectations and safety culture is led from the top. All employees globally, including Board and Executive Team members, receive training in the JTZH program.
In 2021 we published our overarching company JTZH strategy defining the expectations and responsibilities of our corporate, business, regional and local management teams in the implementation of the program.
All manufacturing facilities are subject to a monitoring visit to assess how well the program is being embedded at each site. JTZH coordinators were appointed at all non-manufacturing locations globally to support the roll out of training packages and collate engagement data.
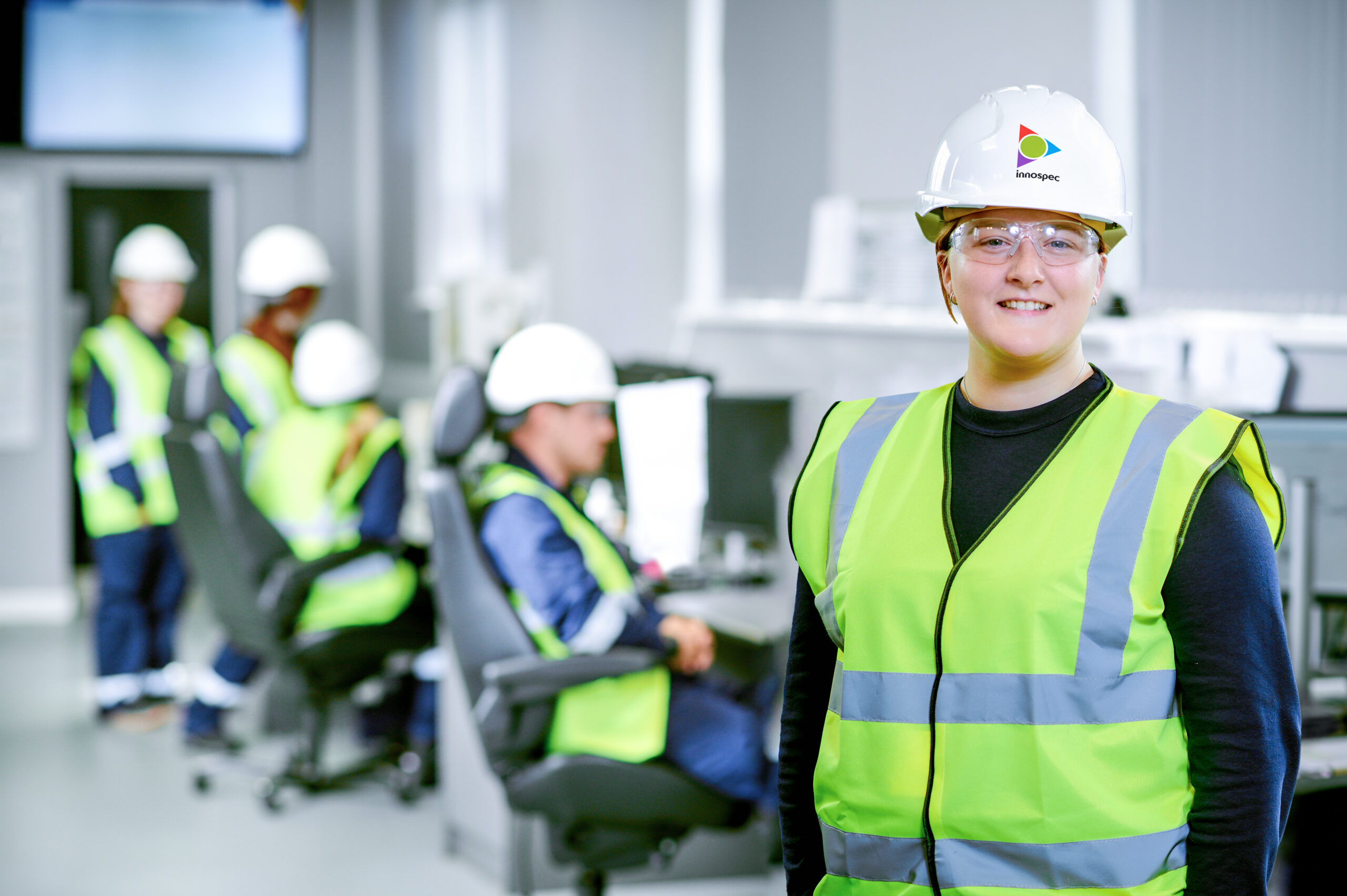
JTZH training modules
Our Hazard Awareness Training modules are designed to target the most common causes of accidents occurring at Innospec. The modules are translated into our five core languages and supported with a range of promotional materials to aid communication on site. We have completed the global rollout of three hazard awareness modules to all employees:
- In the line of fire
- Slips, trips and fallsĀ
- Working at height
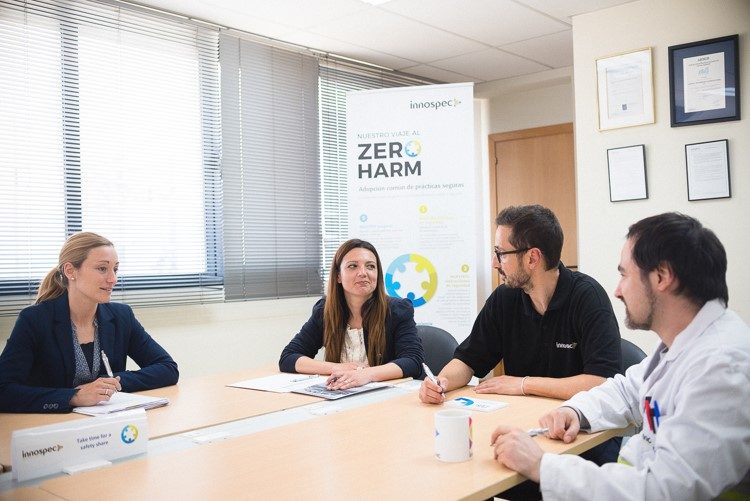
Other JTZH training packages we have rolled out to specific functions include:
- JTZH manufacturing refresher course
- JTZH office refresher course
- General office SHE awareness course
These courses are designed to help further embed the program at manufacturing sites locally and promote engagement and understanding in office-based locations.
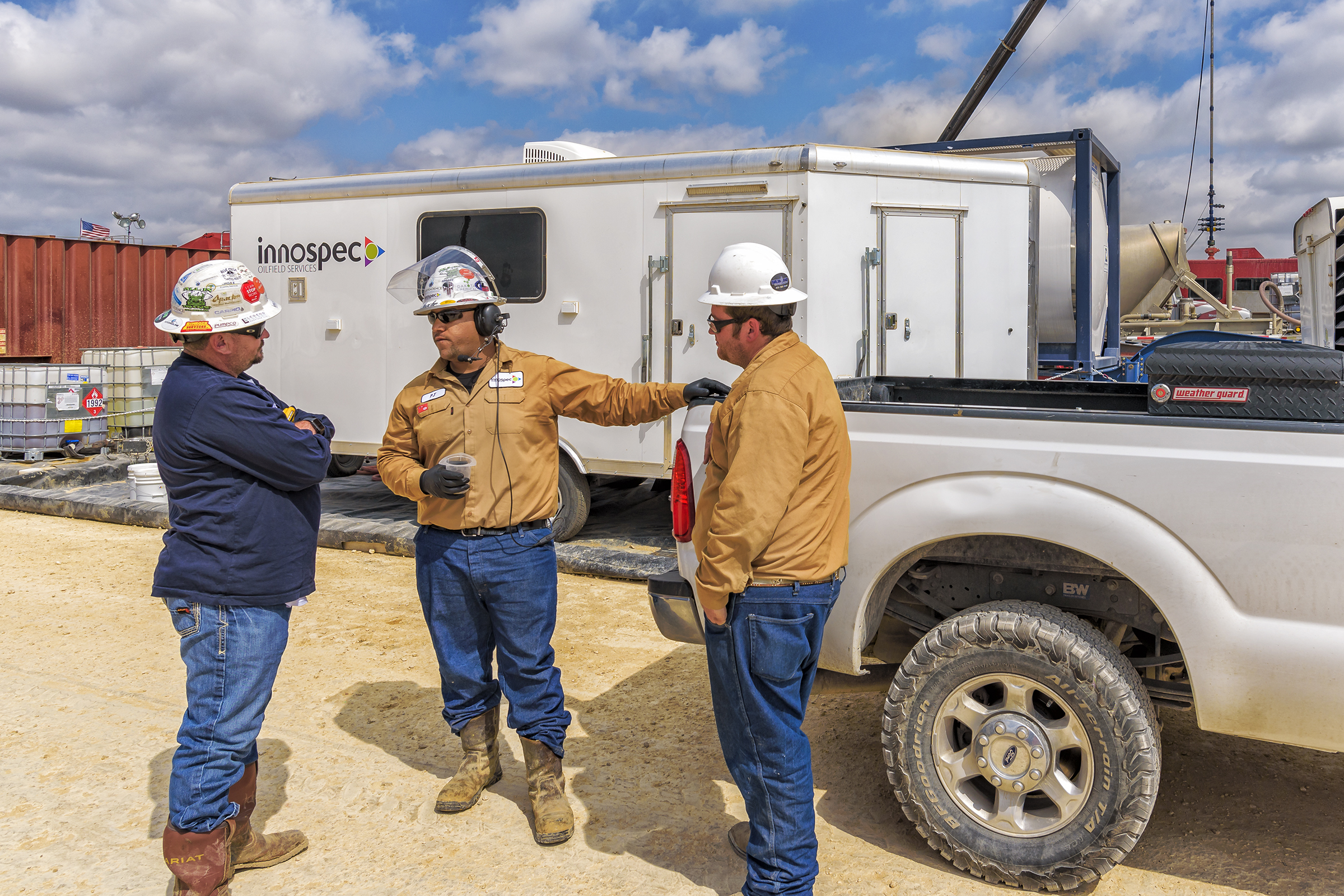
Site initiatives supporting behavioural safety
Each year our sites maintain existing programs or introduce new initiatives to help improve safety at a local level.
In 2024, our Leuna team in Germany collaborated with an external consultant to help increase employee safety awareness and identify areas for improvement. Following two employee safety workshops, participants highlighted the need to place greater emphasis on contractor safety and to further develop the format of safety communications used on site. Going forward, plant managers will share more safety information digitally with employees to improve engagement and efficiency. Additionally, ‘safety’ is now a permanent topic of discussion during shift meetings.
Internal employee recognition
Several of our locations operate a ānear miss of the month or quarterā scheme to encourage employees to report near misses:Ā
- Our Midland, Oklahoma and Pleasanton sites in the US reward employees reporting ānear miss of the monthā and ānear miss of the yearā with prizes such as branded jackets and caps.Ā
- We also choose a āsafe employee of the yearā for each US region, recognizing those who have excelled in SHE functions, and present regional and departmental awards for achieving zero recordable accidents, no vehicle incidents and no lost time accidents, within the year.
Journey To Zero Harm in 2024
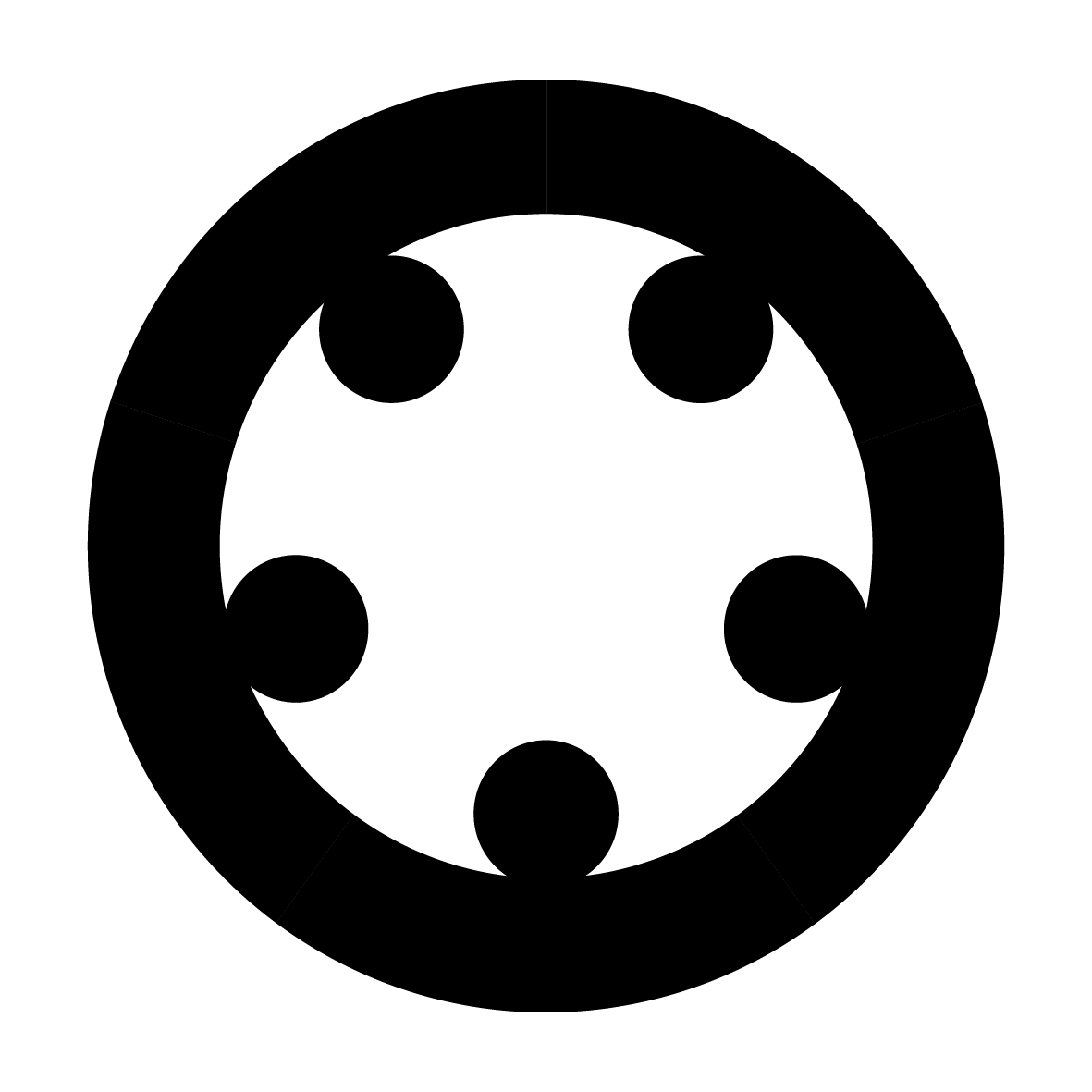
Eight-year
milestone reached of our JTZH program
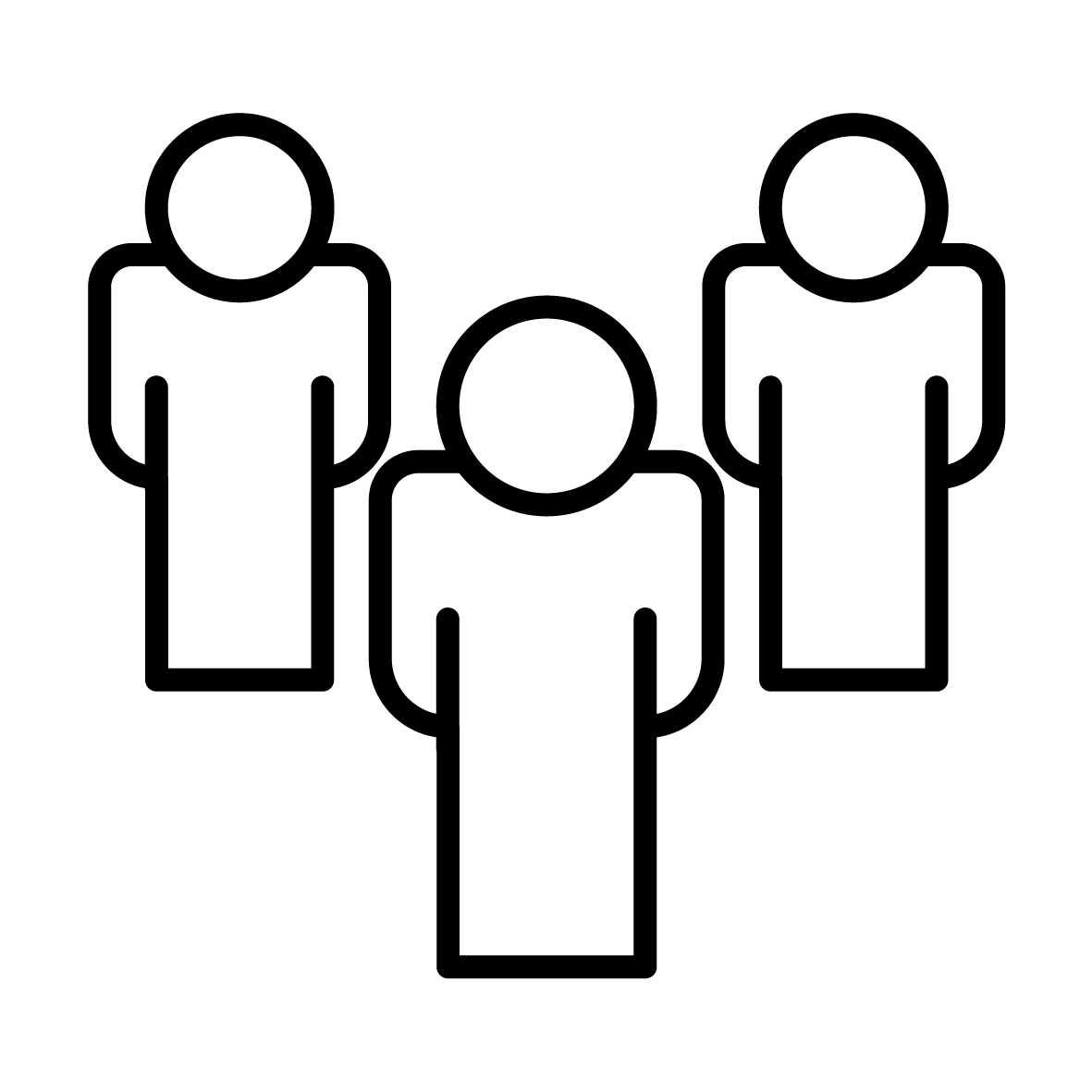
12,570
safety interactions completed
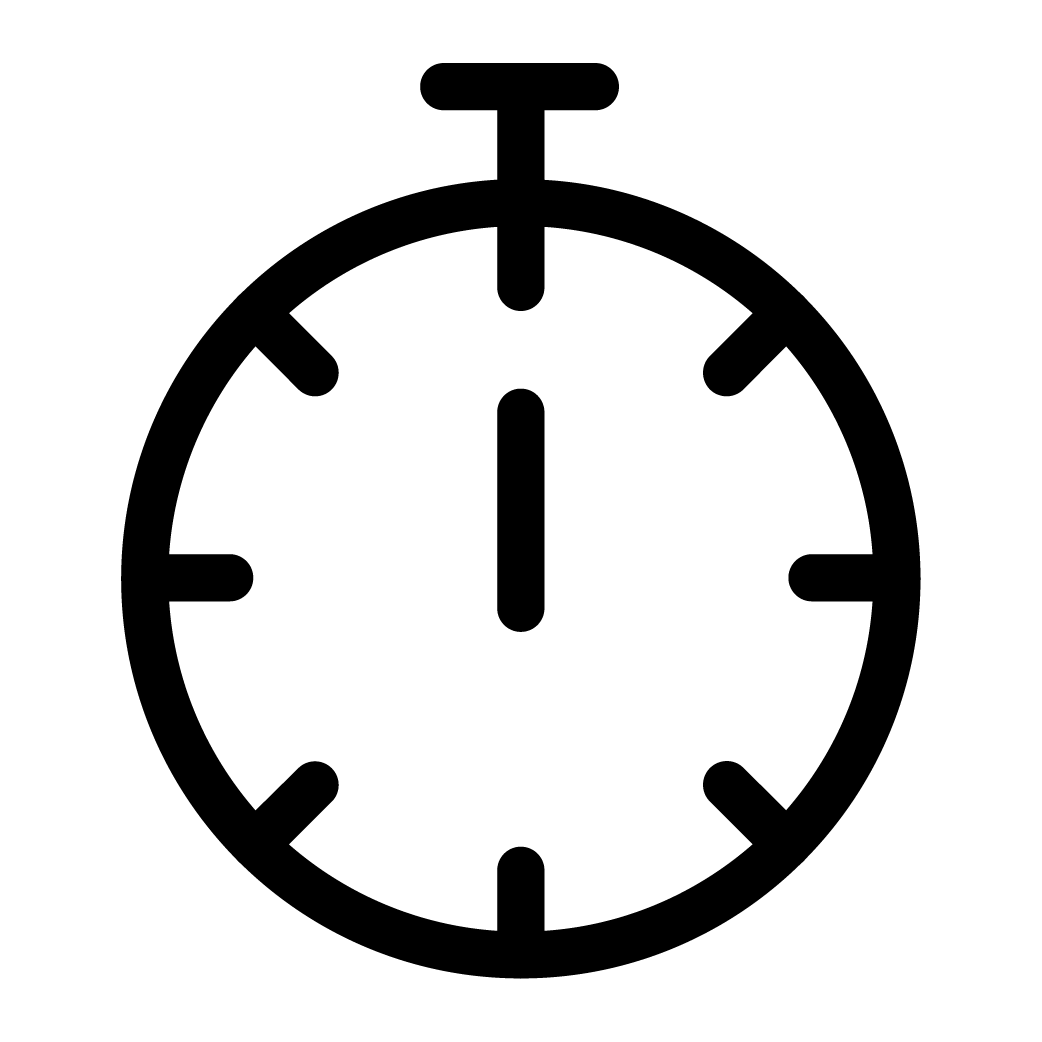