Our process safety management
- Process safety standards
- Process safety audits
- Process safety performance indicators (PSPIs)
Risk assessment – Identify hazards and critical control measures
Safe operation – Integrate critical control measures into operational procedures
Management of change – Eliminate risks from changes to existing critical control measures
Safe maintenance – Maintain the integrity of critical equipment and process controls
Incident investigation – Identify root causes to prevent recurrence
Emergency response – Minimize emergency impacts
Competency – Train and assess staff for competence in required activities
Management of contractors – Manage contractors effectively to ensure safety for all involved
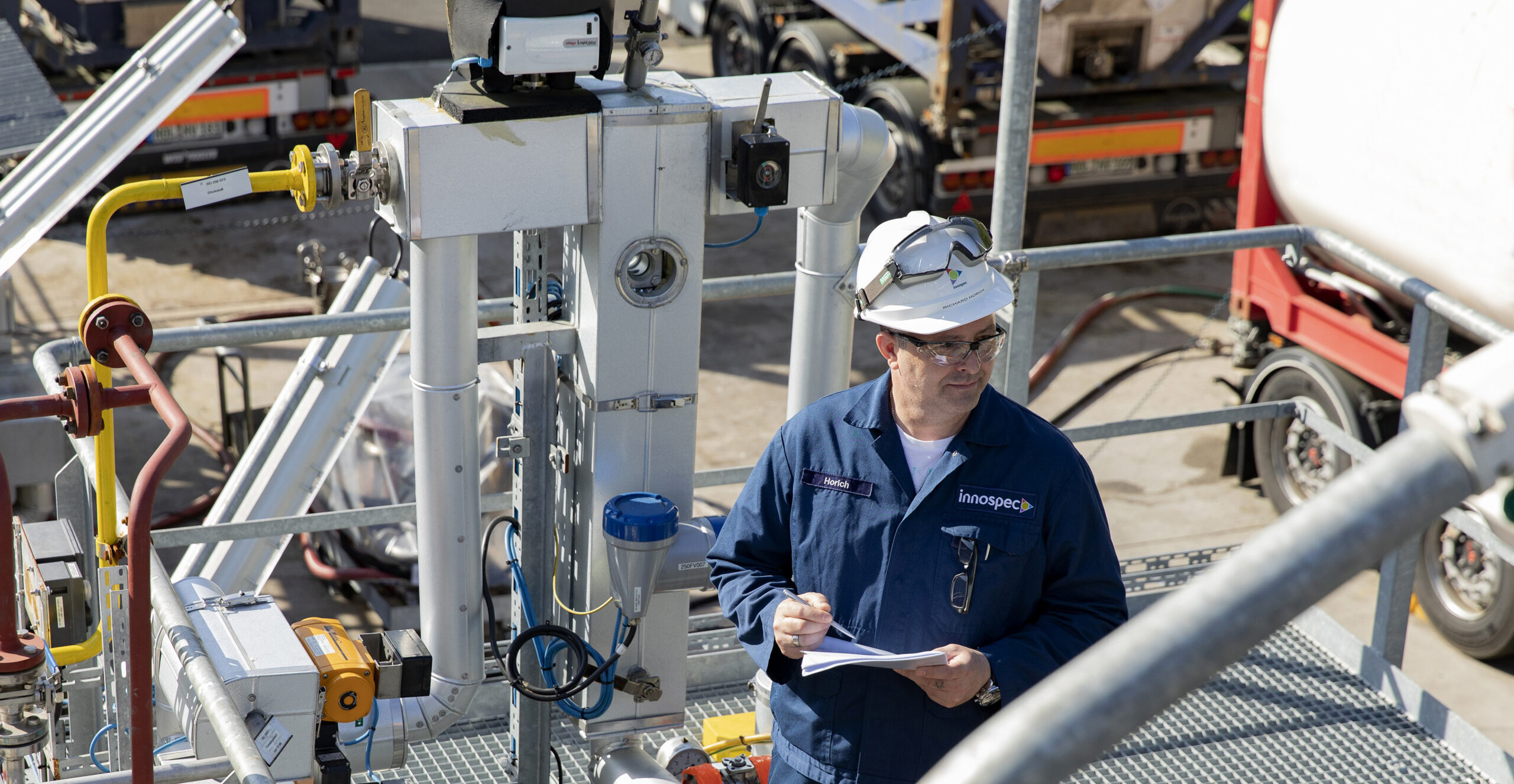
- Compliance with the process safety standards is monitored through process safety audits, carried out by our Corporate SHE team.
- These audits measure a siteās compliance against the corporate standards to establish the degree of implementation and operational employee awareness and to assess critical control measures.
- The outcomes of the audits are discussed during the quarterly Responsible Care Executive Committee (RESPECT) meetings.
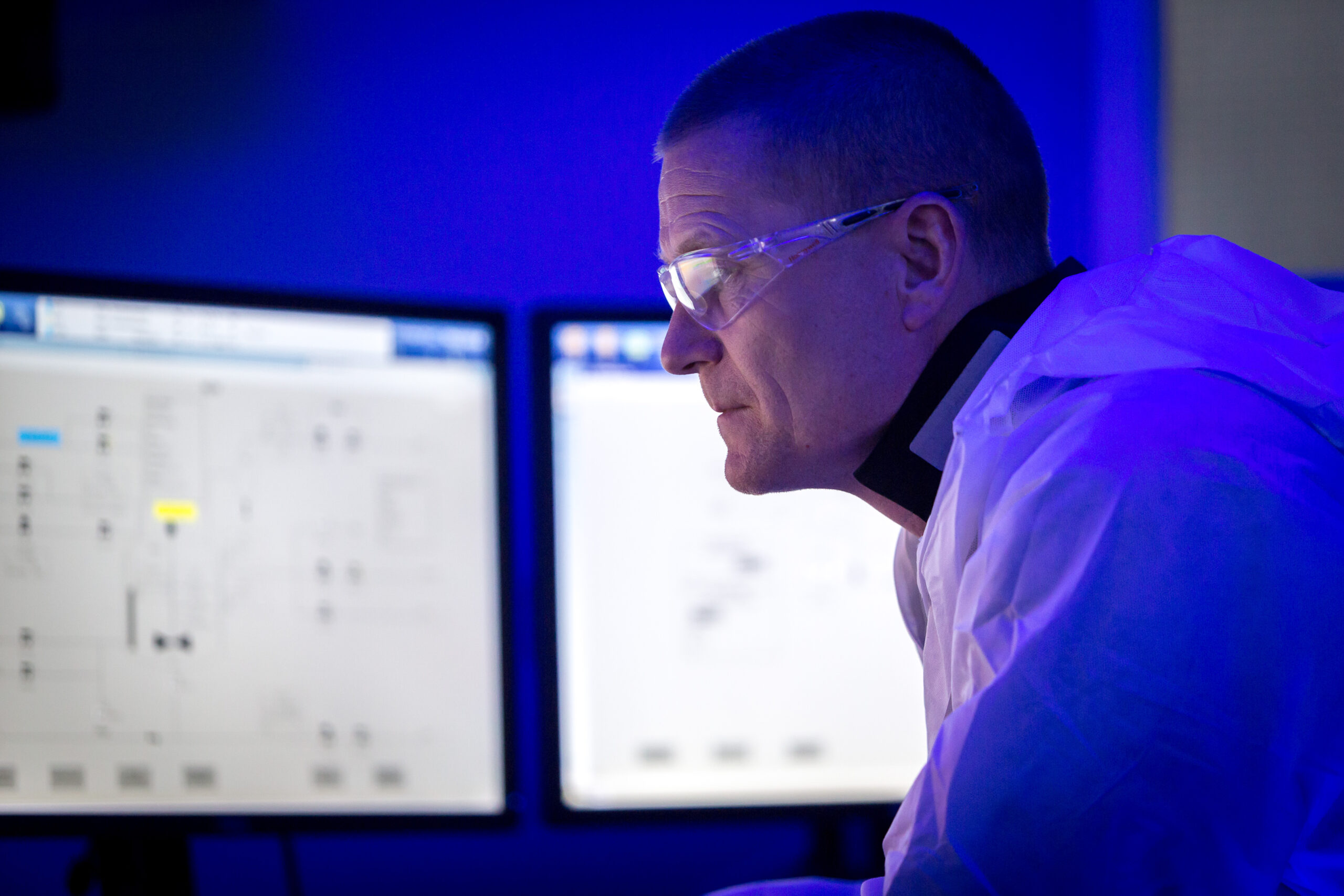
- PSPIs are monitored at site level and are used to determine the effectiveness of all programs and activities that are targeted at reducing process safety incidents.
- The PSPIs are reviewed during the quarterly Responsible Care Executive Committee (RESPECT) meetings and are used to identify any areas of process safety management that need further focus or support.
- Process safety leadership
- Start-up authorisation (SuA) procedure
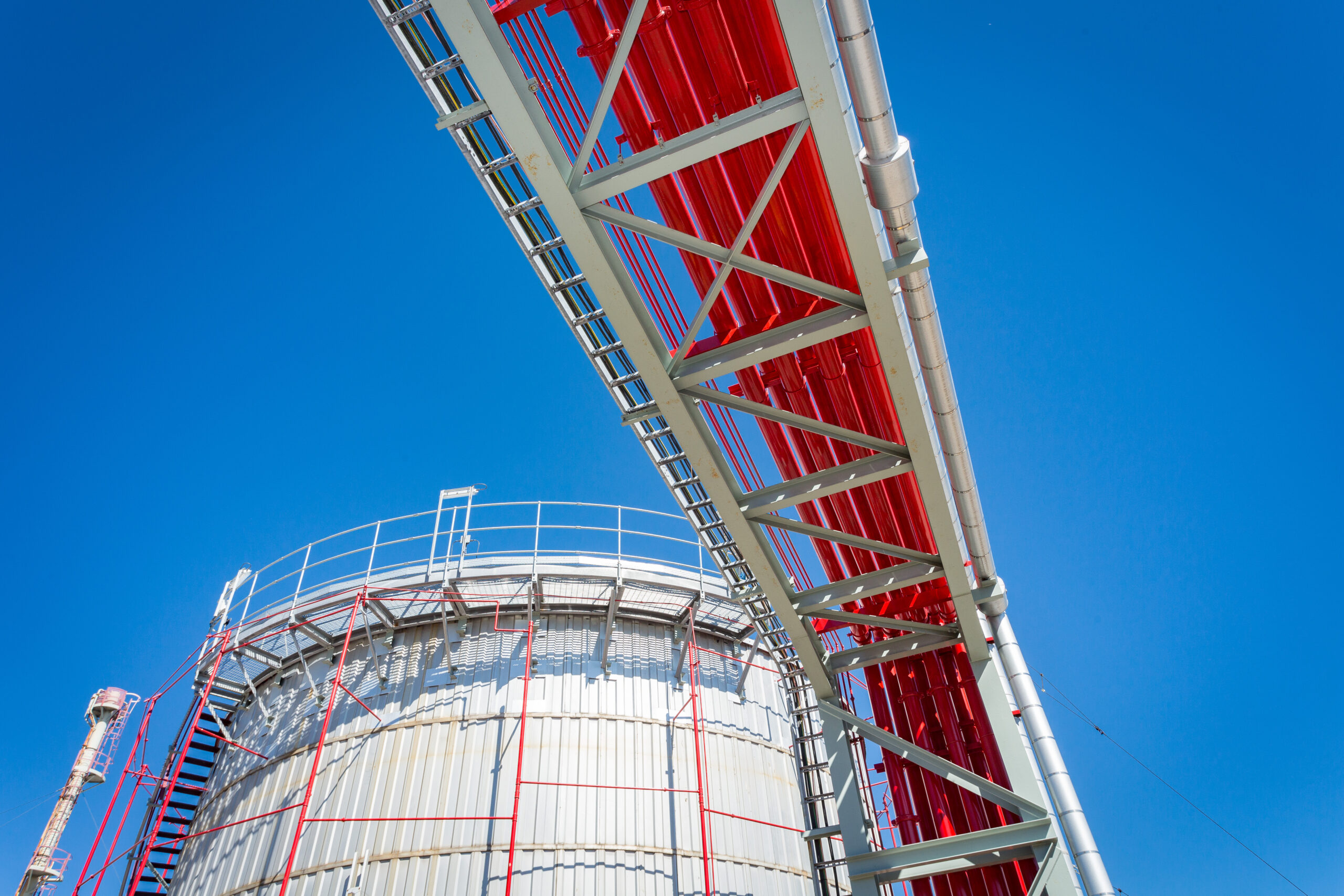
Process safety leadership program involves the Executive Team undertaking personal on-site visits focused on process safety demonstrating, at a local level, our Executive Teamās commitment to the prevention of incidents and accidents.
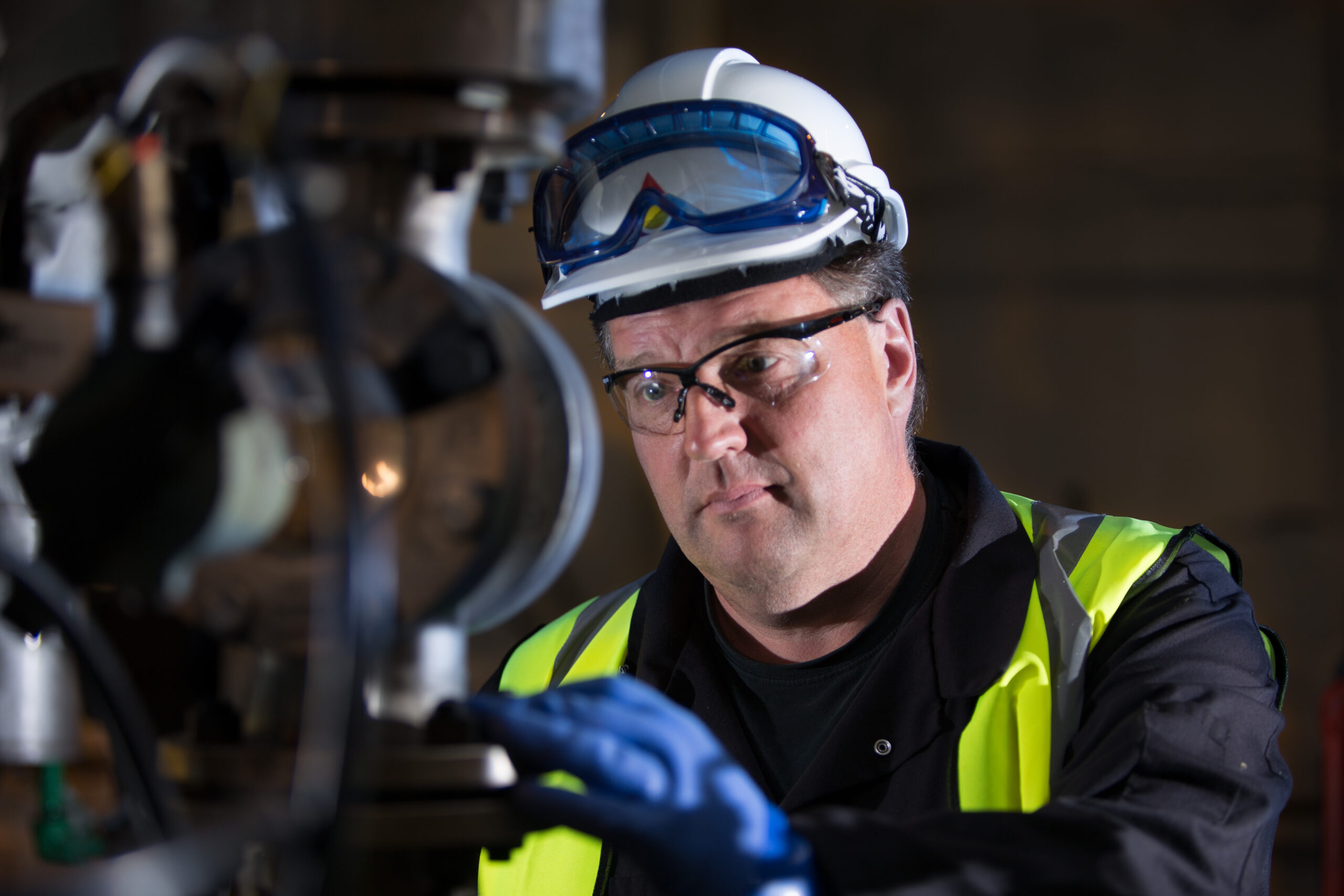
- Launched in 2019, our SuA procedure is used to assess and confirm that process safety will not be compromised following the introduction of new products, processes or major modifications.
- The procedure uses a customized electronic platform to enable all appropriate safety and design issues to be considered, collated, reviewed, approved and documented prior to commissioning.
- The SuA platform has been recently extended to capture key safety and design information for existing products, allowing sites to securely upload existing product dossiers so that they can be accessed and reviewed centrally.
- At the end of 2024, there were 250 approved product dossiers registered on the SuA platform.
Preparing for emergencies
All our manufacturing sites need to be ready to provide a safe and competent response to an onsite emergency. For each site we have identified the potential emergency scenarios and documented site emergency response plans. All employees are trained in the contents of the plan and take part in practical exercises relevant to their role in the event of an emergency.
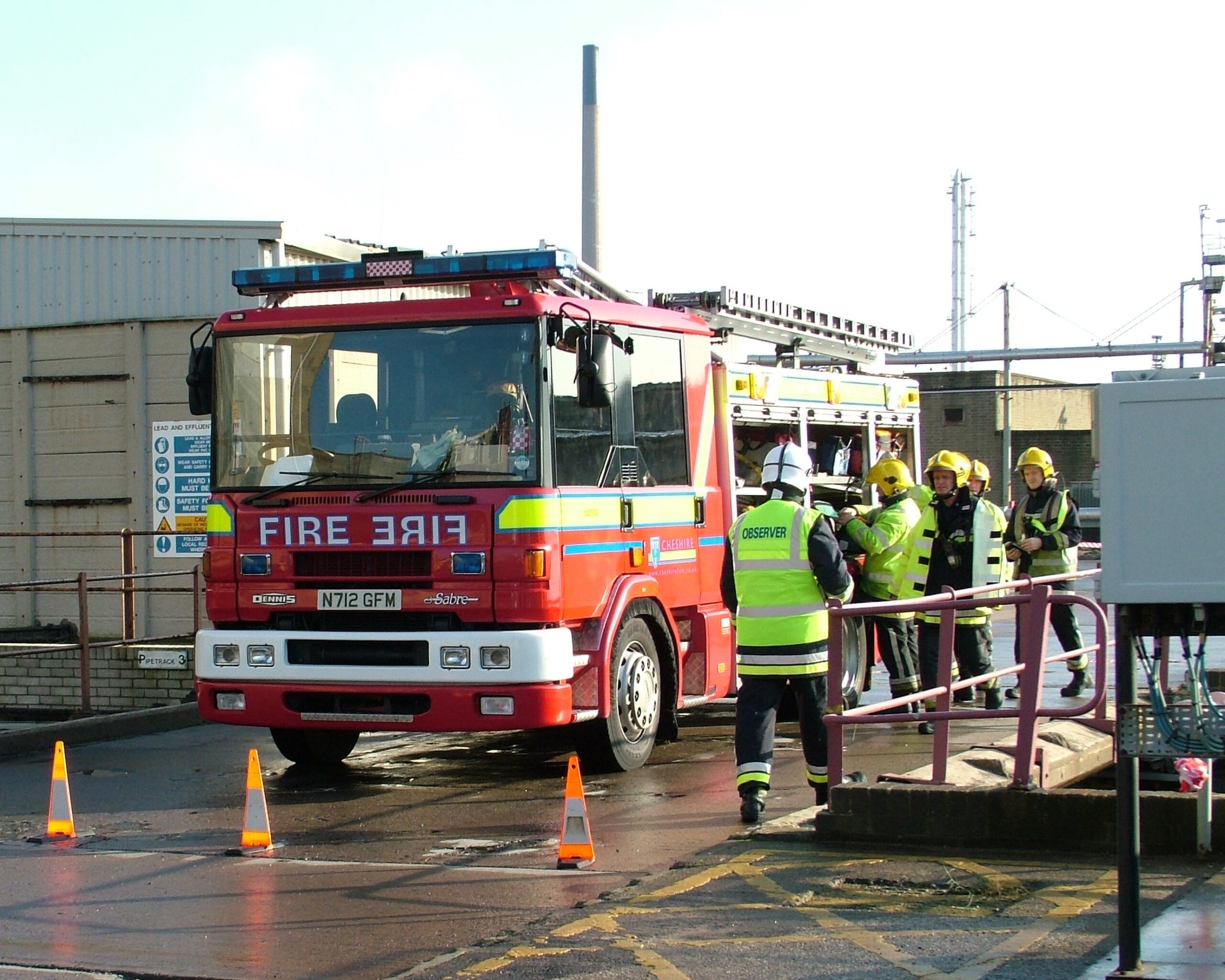
Stakeholder Preparation for Emergencies
Periodically, emergency training also involves the local emergency services. In 2024, our site in Pleasanton, US, conducted on-site emergency response training with the local fire department. In Salisbury, US, our team met with multiple members of the emergency response community to hold a communications exercise and site walk through. Local fire departments, emergency services, rescue squads and state highway patrol all participated. Exercises like these enhance coordination and communication between us, the emergency services, and the community in which we work and live.
We have partnered with Chemtrec in the US and Canada and Carechem 24 for all other global locations to provide emergency response support in the event of an incident involving one of our products, either during transportation to or at our customersā premises. They offer multilingual, 24/7 emergency response helplines and are staffed by trained chemists, with access to a complete library of our Safety Data Sheets, to enable them to provide initial support in dealing with incidents.
Loss of Containment (LOC) events
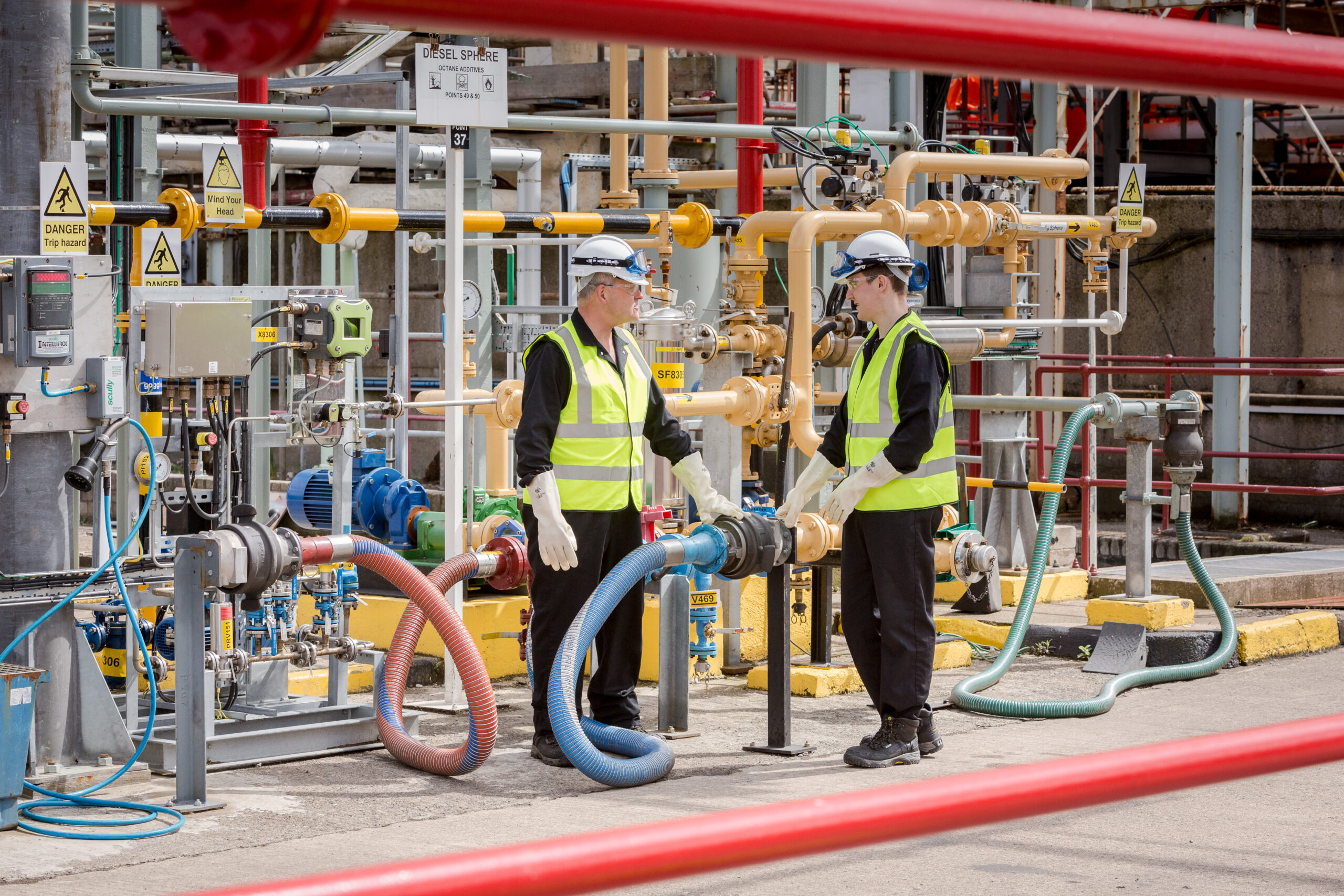
Addressing Loss of Containment (LOC) chemical releases and spills
We take the safe containment of process materials handled at our manufacturing facilities very seriously. All unintentional chemical releases and spills are reported, tracked, regardless of the quantity involved or the nature of the material involved. We investigate them fully so we can understand exactly what has happened and remedy any underlying issues. All manufacturing facilities must develop and implement a LOC reduction program. Performance across the group is reviewed quarterly during the RESPECT meetings.
In 2024, across our global operations, there were 428 individual spillages resulting in a total loss of 129,000 kg of material. Of these events, 155 involved losses of less than 1kg.Ā None of the spillages were required to be reported to the local regulator in 2024.
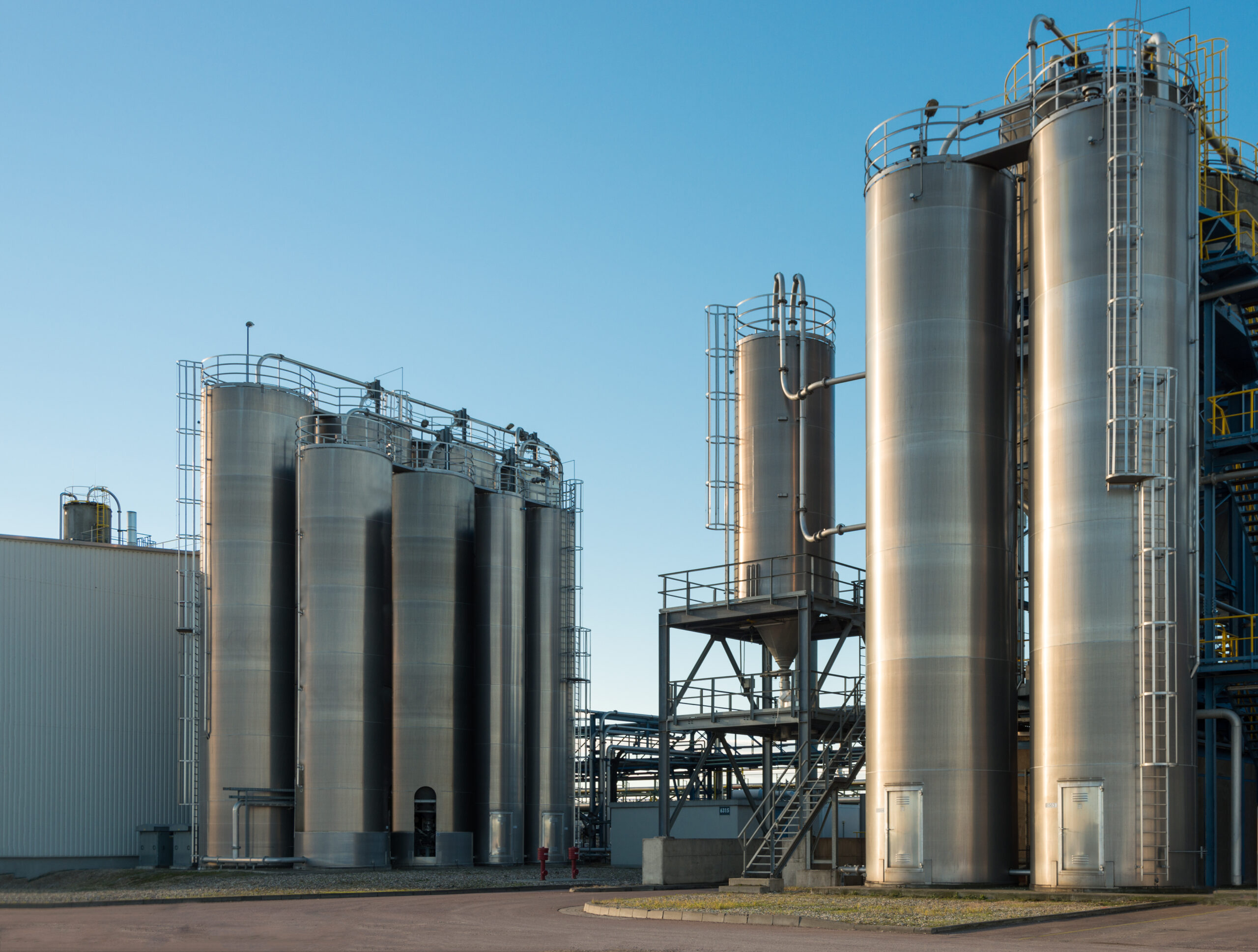
Preventing Loss of Containment (LOC) chemical releases and spills
Regional review teams and dedicated LOC improvement teams at all our sites help to identify trends, discuss challenges and share best practice in LOC prevention. Actions taken to prevent LOC events have included monthly plant tours to identify potential areas of risk. We also used drone technology for the first time in 2024 to support our storage tank inspection program. LOC communications have been enhanced through the introduction of face-to-face briefings, displaying performance indicators and event posters in control rooms, conducting spot audits, and discussing LOC events during quarterly safety meetings.
In 2024, these actions resulted in a 26% reduction in the total number of ‘more than minor’ LOC events, with 129 metric tonnes in quantity lost.