2024 Performance
- Energy Use
- Greenhouse Gas Emissions
- Air Emissions
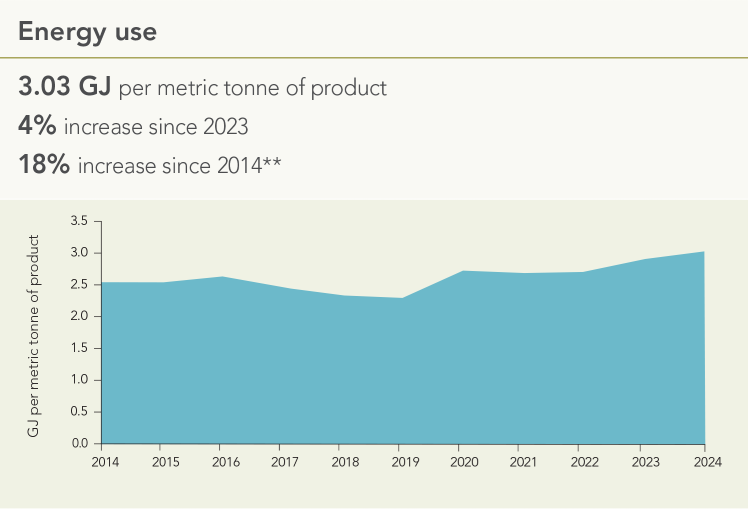
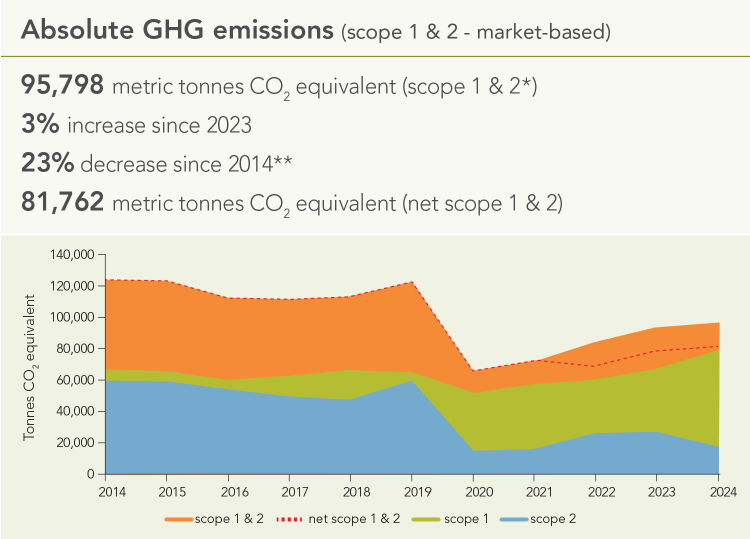
The new combined heat and power (CHP) plant installed at our Ellesmere Port, UK, site operated for the full year compared to only the final quarter of 2023. During the commissioning period, the plant was only producing electricity and a small amount of steam. This meant that steam and hot water required by the site was generated by the concurrent operation of the site’s existing natural gas fed boiler. As expected, this dual operation resulted in an increase in natural gas consumption for the site, resulting in an 18% increase in absolute scope 1 GHG emissions from 2023. Although initially powered by natural gas, the new CHP plant has been constructed so that it can be operated on a 20% hydrogen blend in the medium term and eventually 100% hydrogen, as soon as it becomes available.
In 2024, for the first time, all 14 of our manufacturing facilities procured 100% renewable electricity, resulting in zero associated scope 2 emissions. We are pleased to have achieved this target six years ahead of our 2030 target.
At our Ellesmere Port, UK site a small solar and wind energy station generated 7,959 KWh of physical renewable electricity. This renewable energy is used for charging our electric vehicles and powering our illuminated signage. Use of procured and physical renewable electricity now accounts for 19% (93,549 MWh) of our total energy mix.
The remaining scope 2 emissions are associated with the use of procured steam at two of our manufacturing locations. Overall, our absolute scope 2 market based GHG emissions have decreased by 35% compared to 2023 and 71% since 2014.
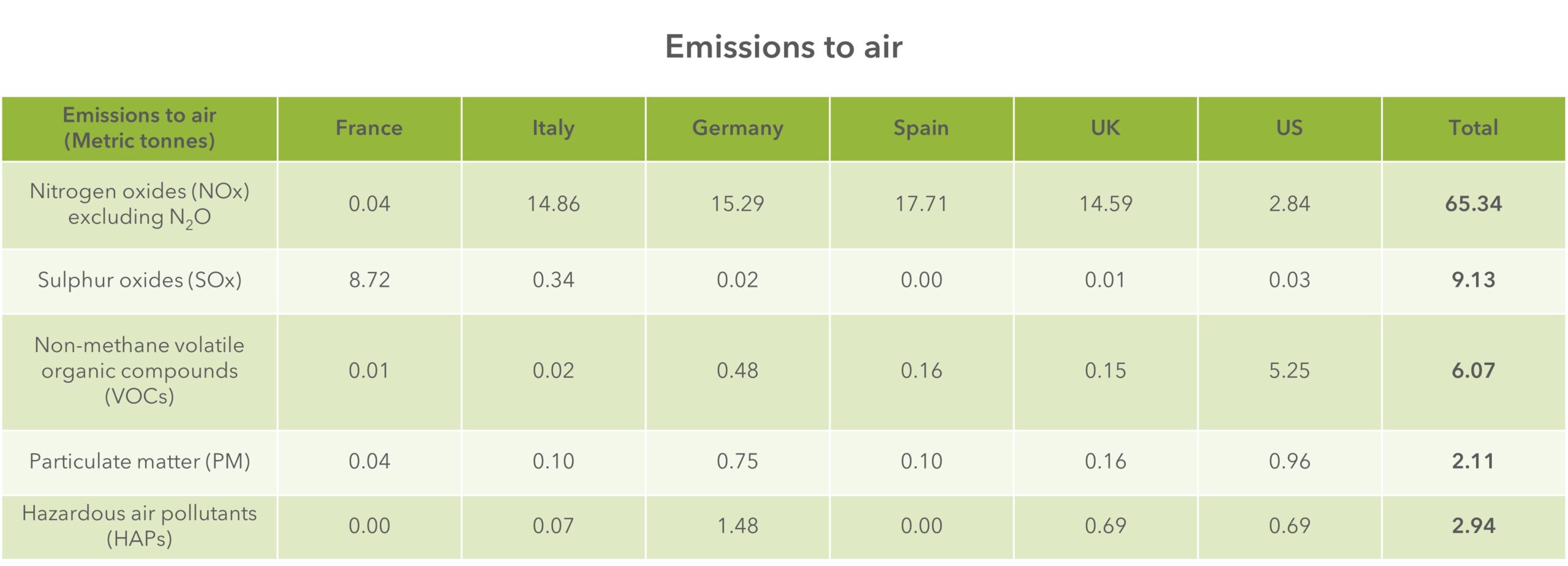
– Emissions to air are monitored differently, depending on the manufacturing site, nature of activities, emissions and source.
– Total annual emissions data is typically taken from continuous monitoring data where available or an extrapolation from one or more sampling campaigns conducted at a site level.
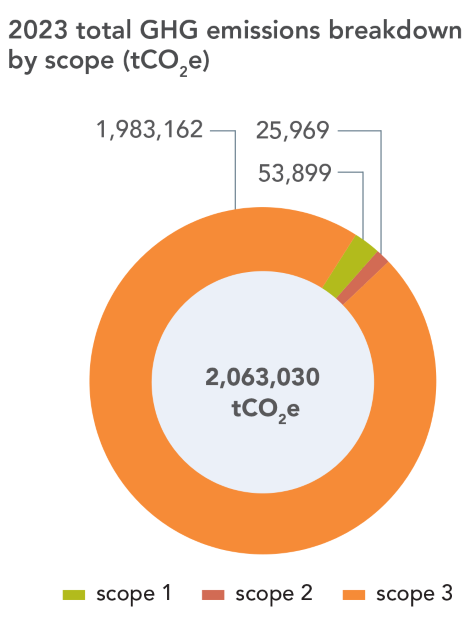
Global Carbon Footprint
In 2024, we completed an assessment of our 2023 global scope 3 emissions. The assessment included 10 applicable scope 3 categories and was in line with the World Resources Institute GHG Protocol and industry best practice. The remaining five categories were excluded on the basis that they were either not applicable or not required. We improved our calculation methodology and output by acquiring consumption data for all global reporting units and refining the accuracy of emission factors used for raw materials, product use and disposal calculations, while using primary data where available.
For our 2023 reporting period, our combined GHG emissions were 2,063,031 tCO2e, which represents a 17% reduction on 2022. Scope 3 emissions accounted for 96.1%, scope 1 for 2.6% and scope 2 for 1.3% of our total emissions.
In 2024, we used this information to review viable options and timeframes to develop a credible decarbonization pathway. We looked at process optimization, energy reduction and recovery programs, alongside assessments of renewable sources of energy including biomass, hydrogen and photovoltaic (PV) solar panels. We also considered logistics optimization improvements and increased supplier engagement. Following this review we have committed to setting new GHG emissions reduction targets.
Our Emissions Reduction Targets
Scope 1 and scope 2 emissions
50% reduction by 2034 from our 2014 baseline
Scope 3 emissions
28% reduction by 2034 from our 2022 baseline
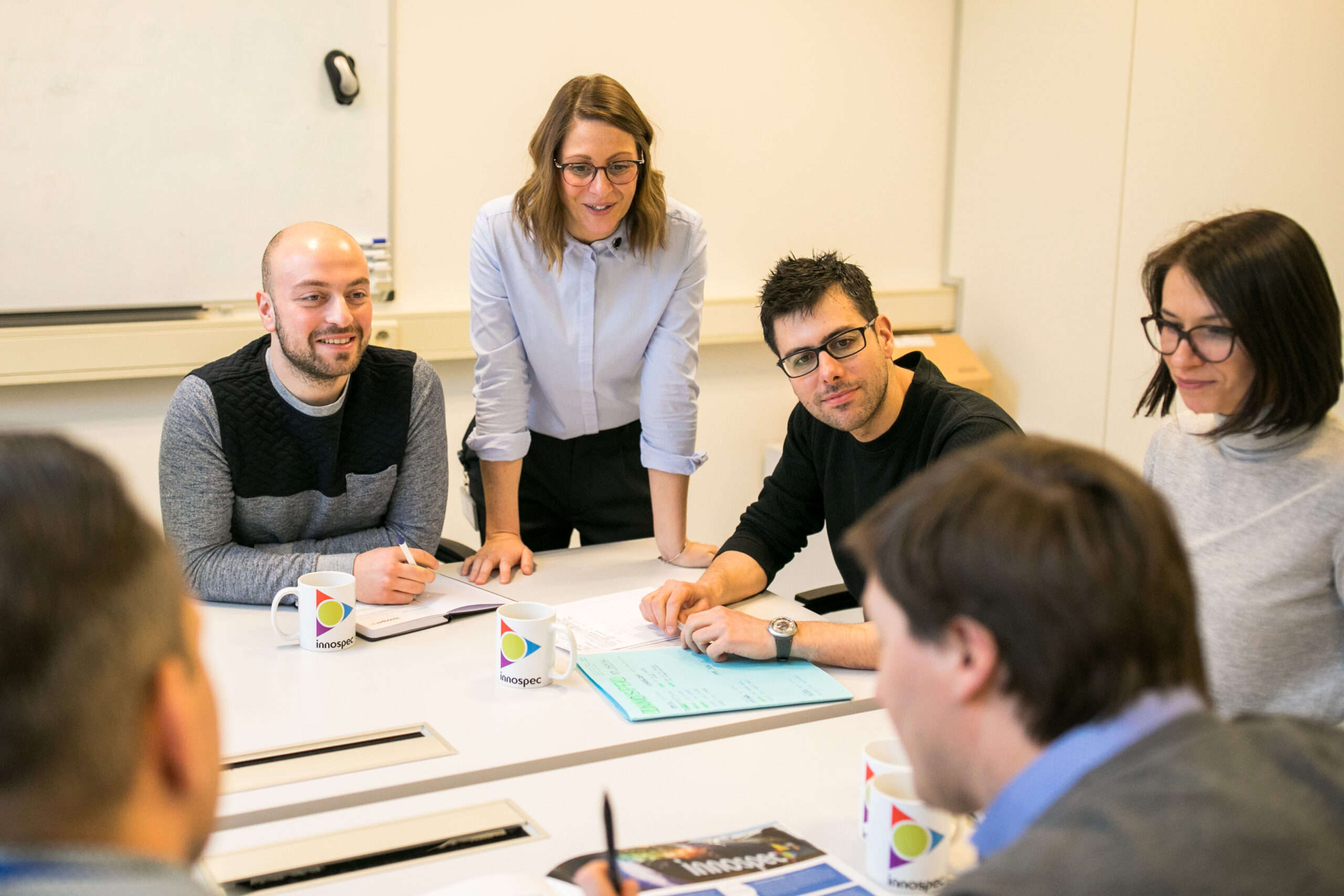
Resource Reduction Group
Established in 2016, our Global Resource Reduction Group (RRG) was set up to develop and share best practice across our 14 manufacturing sites. Its global remit encompasses large capital investments, company-wide projects, and local initiatives. We have a dedicated energy reduction fund to support major projects that will deliver economic rates of return consistent with other organic capital investments, alongside environmental benefits.
The group continued to deliver a pipeline of energy reduction projects in 2024. Moving forward, these initiatives are expected to cut annual energy consumption by 2,289 MWh and reduce total scope 1 and 2 emissions by 367 metric tonnes COā equivalent.
- Midland, US
- Vernon, France
- Leuna, Germany
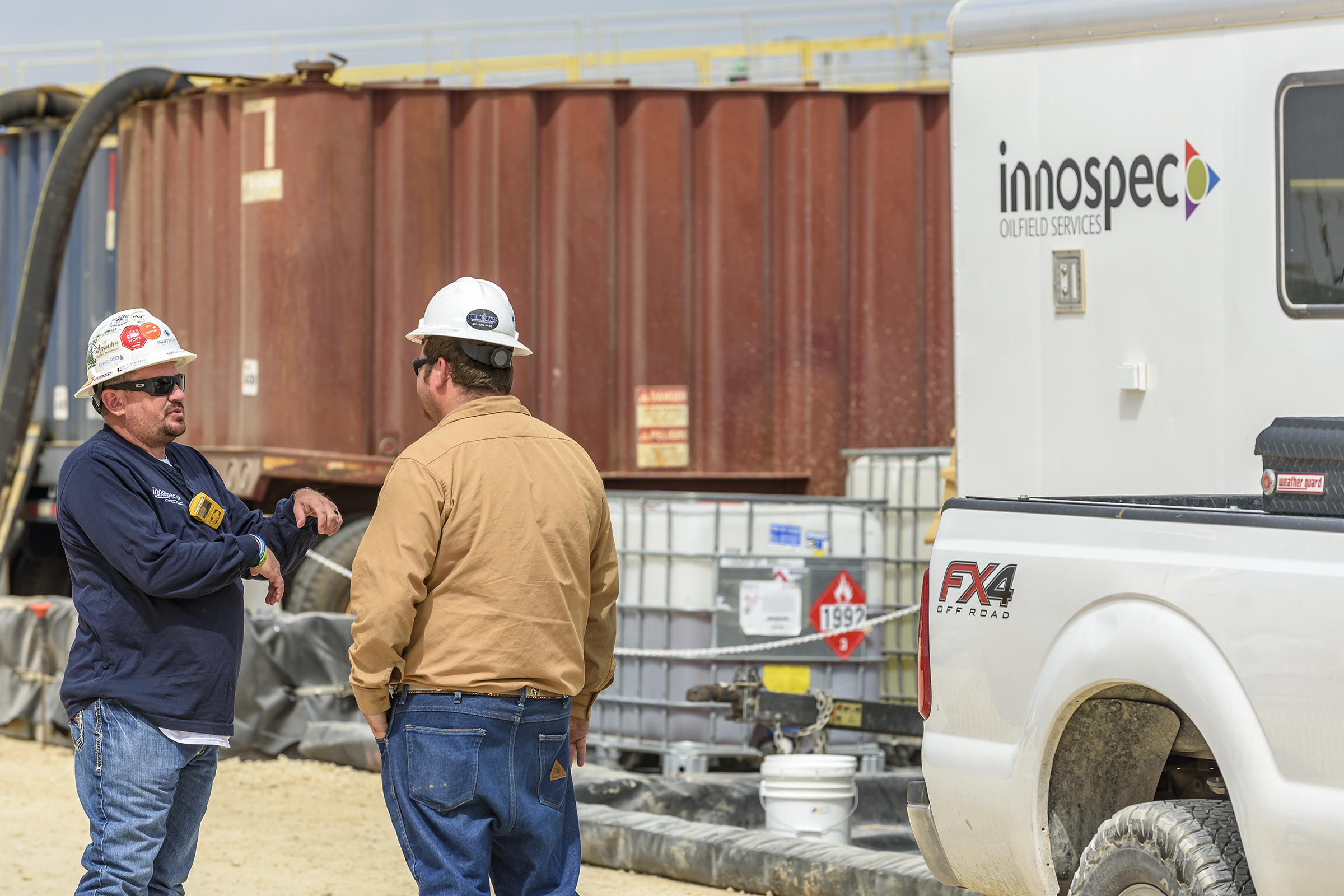
Midland, US
At our site in Midland, US we replaced our diesel-powered air compressor with a more energy-efficient electric model to reduce energy consumption, maintenance costs, and reliance on fossil fuels. Modern electric compressors are more efficient, recover waste heat, and eliminate the need for diesel fuel, resulting in a smaller environmental footprint. This will result in a saving of 322,000 kWh per year, equating to 83 Tons COāe.Ā
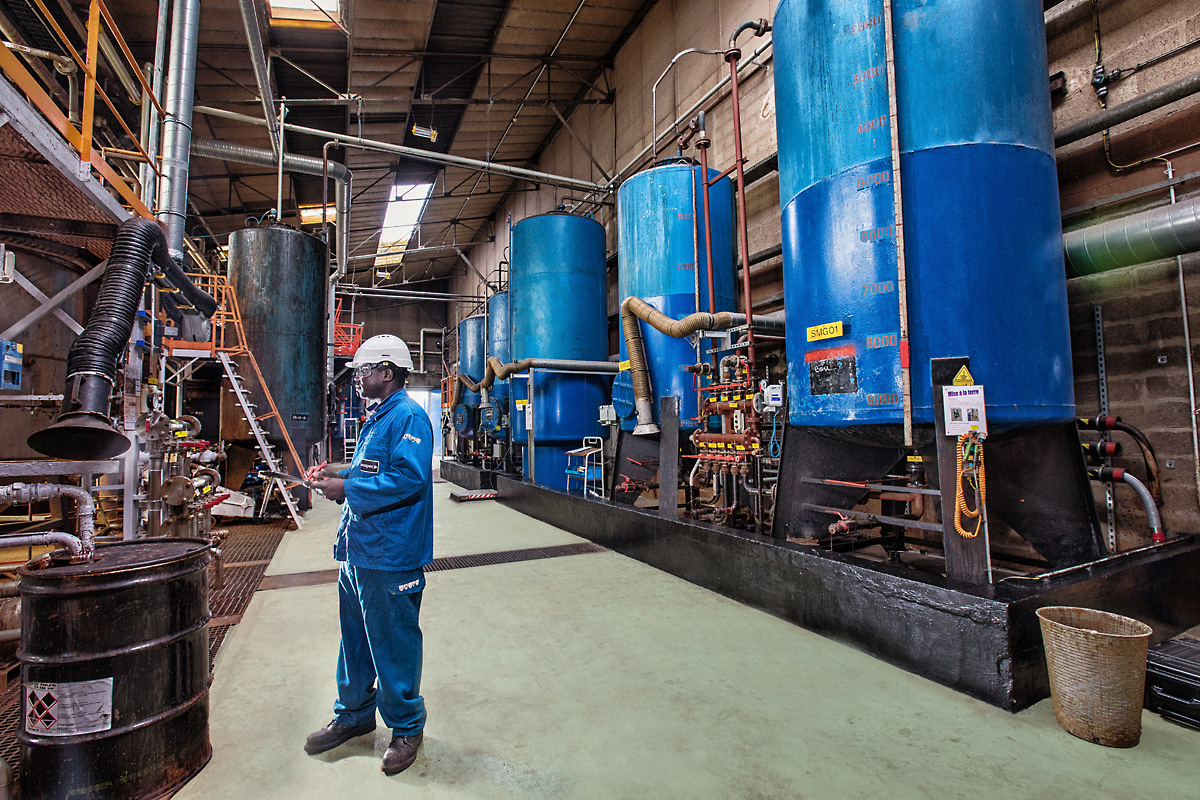
Vernon, France
The installed a heat pump and reversible air condition system. This has helped to reduce energy consumption at the site by 26,428 kWh/year by efficiently transferring heat instead of generating it, and by providing both heating and cooling from a single unit, reducing reliance on separate systems.
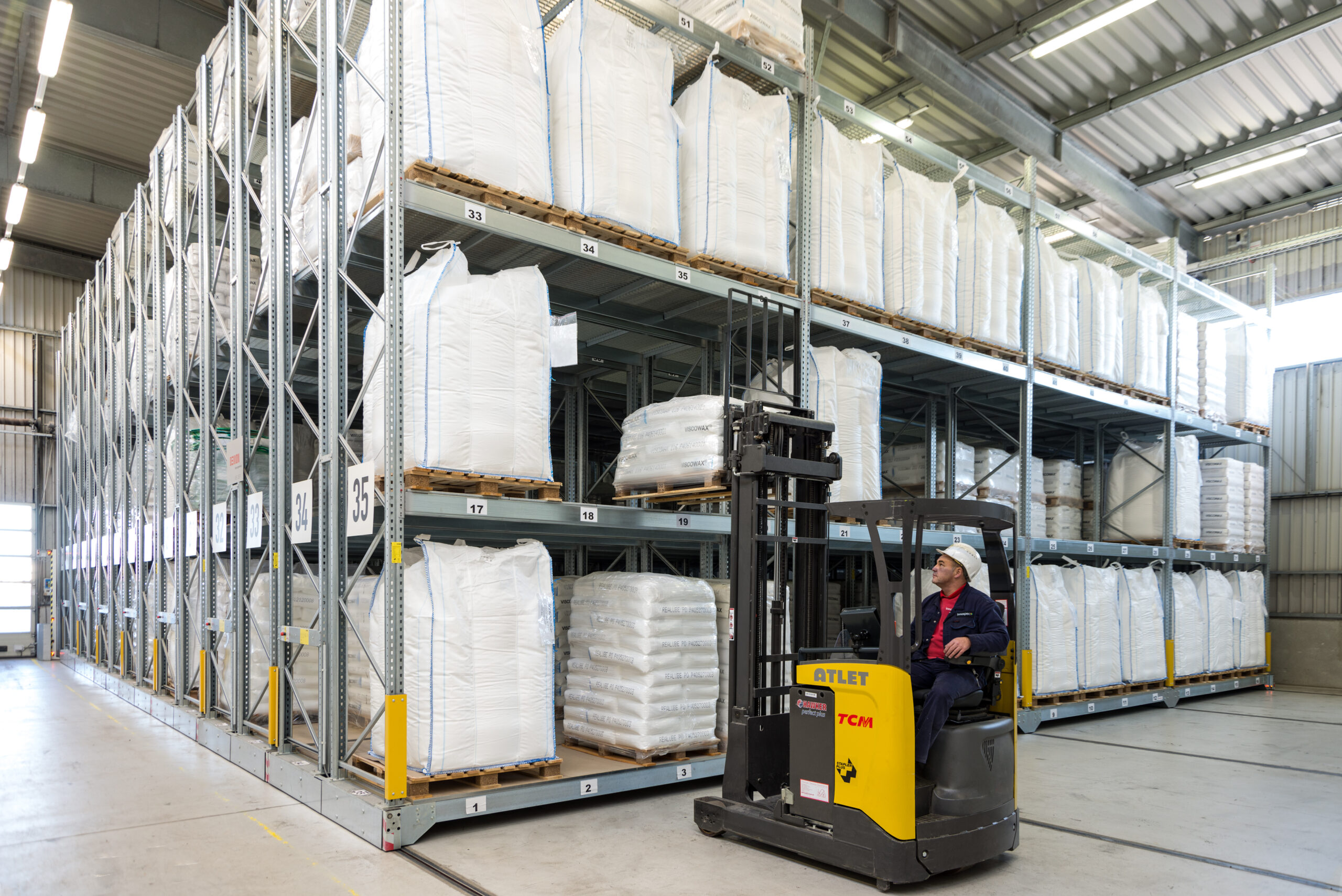
Leuna, Germany
Our site in Leuna identified the opportunity to save 142,275 kWh of electricity per year, or 25.6 Tons COāe, by checking and replacing faulty steam traps. This is crucial for energy conservation in manufacturing as it prevents steam loss, improves process efficiency, and reduces operational costs. Leaking or malfunctioning steam traps allow valuable steam to escape, leading to wasted energy and increased operational expenses.
- Ellesmere Port, UK
- Herne, Germany
- Castiglione, Italy

Oilfield sites, US
Our Oilfield Services business has begun utilizing solar-powered pumps to transfer chemicals from delivery trucks directly to our customersā storage tanks. This has eliminated the need for fuel-operated pumps, saving 243,000 kWh and 53.5 Tons COāe every year. This also creates a safer working environment, by operating with an enclosed, quieter engine.
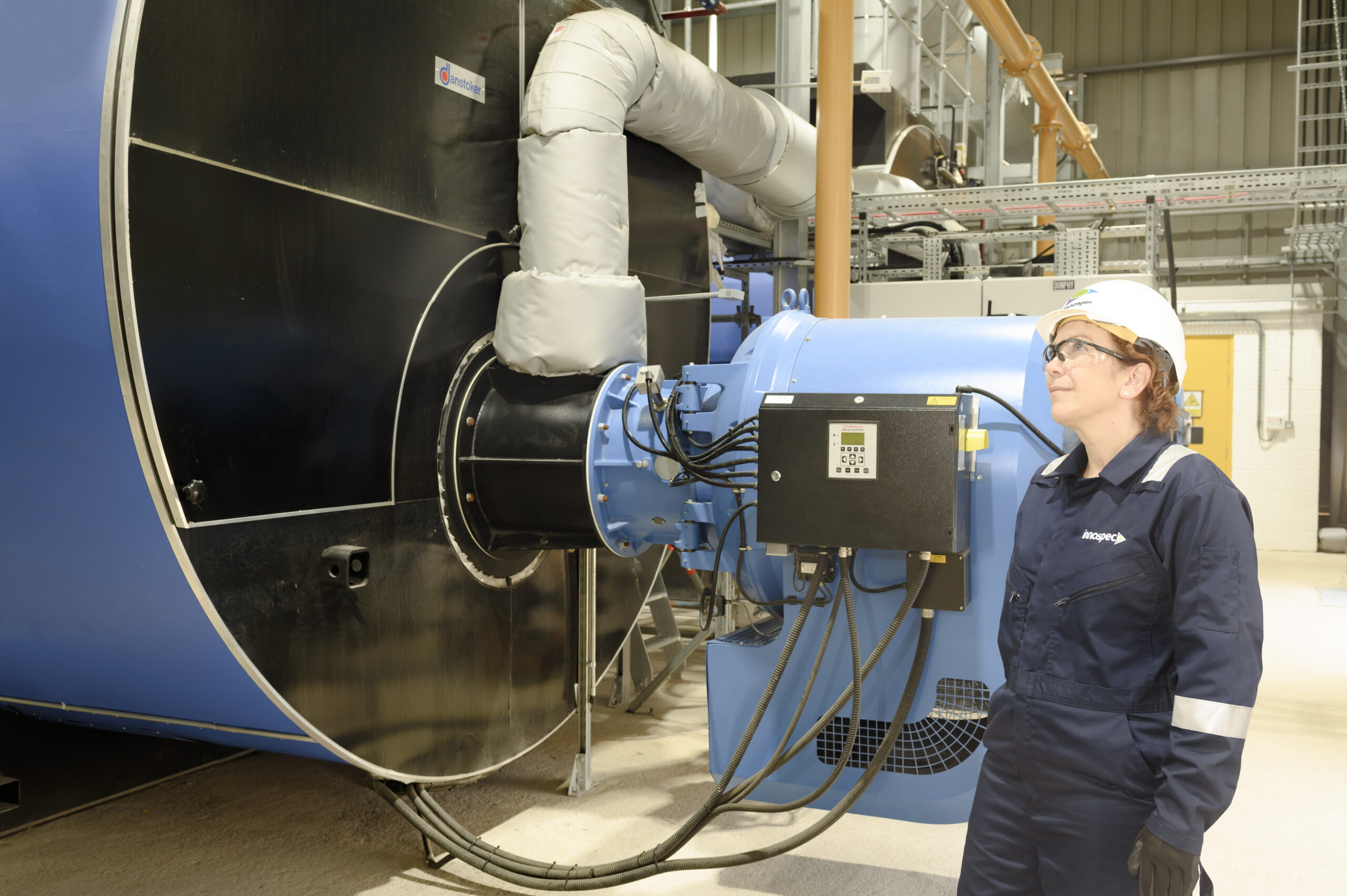
Ellesmere Port, UK
The new combined heat and power (CHP) plant installed at our Ellesmere Port, UK, site operated for the full year in 2024. Although initially powered by natural gas, the new CHP plant has been constructed so that it can be operated on a 20% hydrogen blend in the medium term and eventually 100% hydrogen, as soon as it becomes available. Once the CHP boiler is fully operational, we will be able to decommission the natural gas fed boiler, reducing scope 1 emissions for the site.
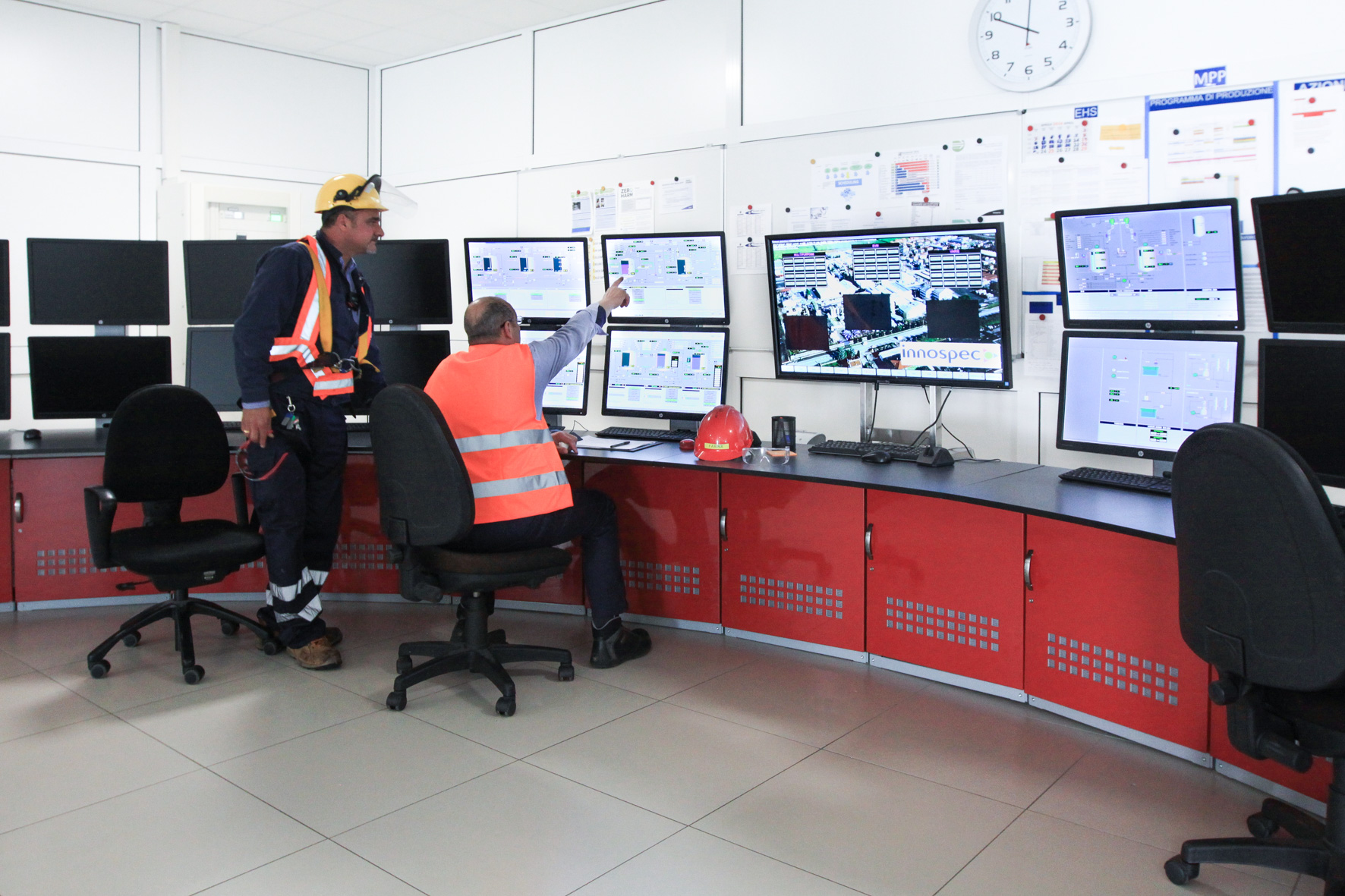
Castiglione, Italy
Our sit in Castiglione has started using a biosafe lagoon system to achieved a saving of 244,000 kWh of electricity and 44.6 Tons COāe per year. This is achieved by providing a sustainable source of heat or biogas for energy generation. The system produces biogas through anaerobic digestion of organic waste, which is then used to generate electricity and heat for the manufacturing processes. Additionally, the heat generated during the anaerobic digestion process is captured and utilized, further reducing reliance on traditional energy sources.