- Total Waste
- Waste Handling Routes
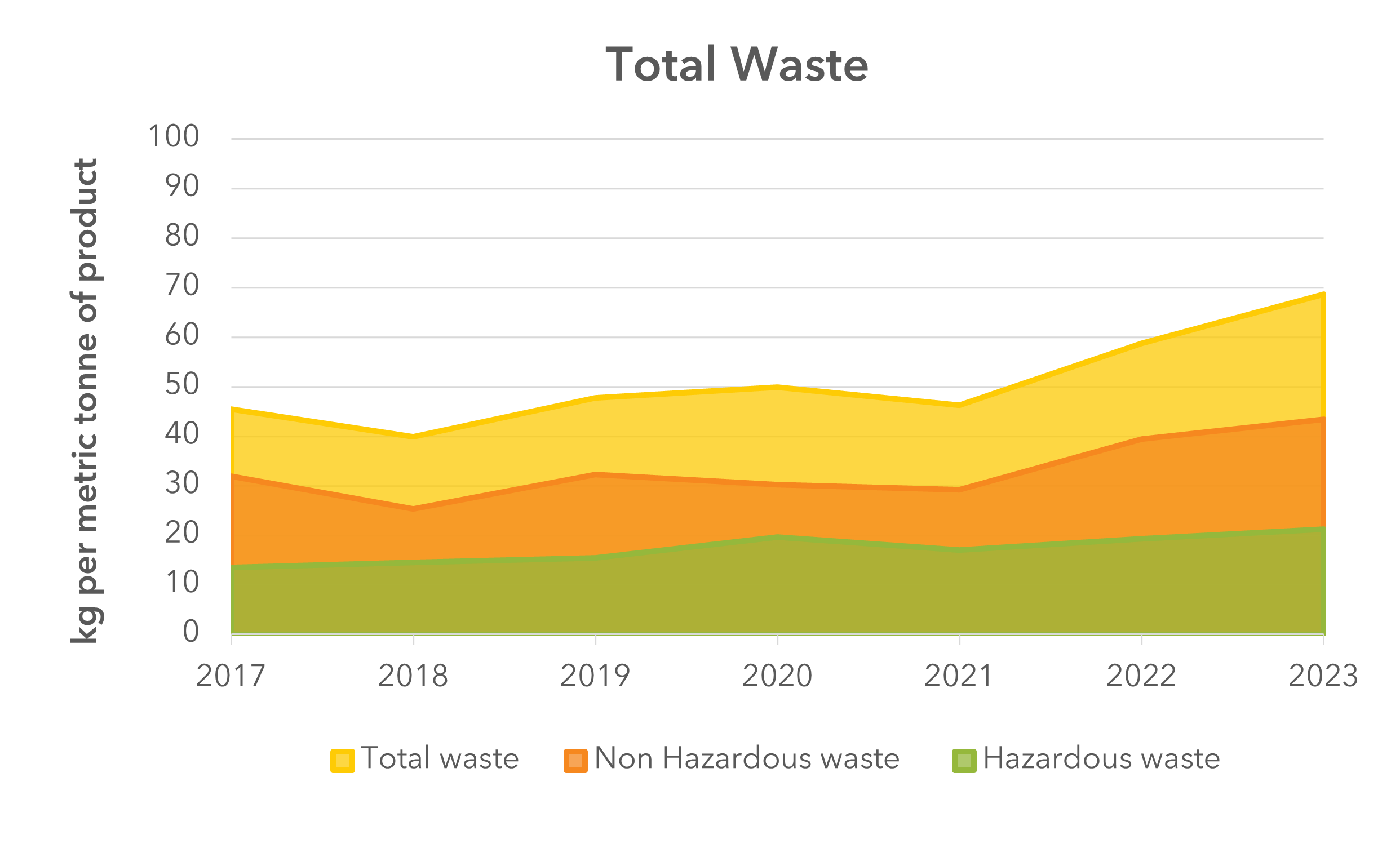
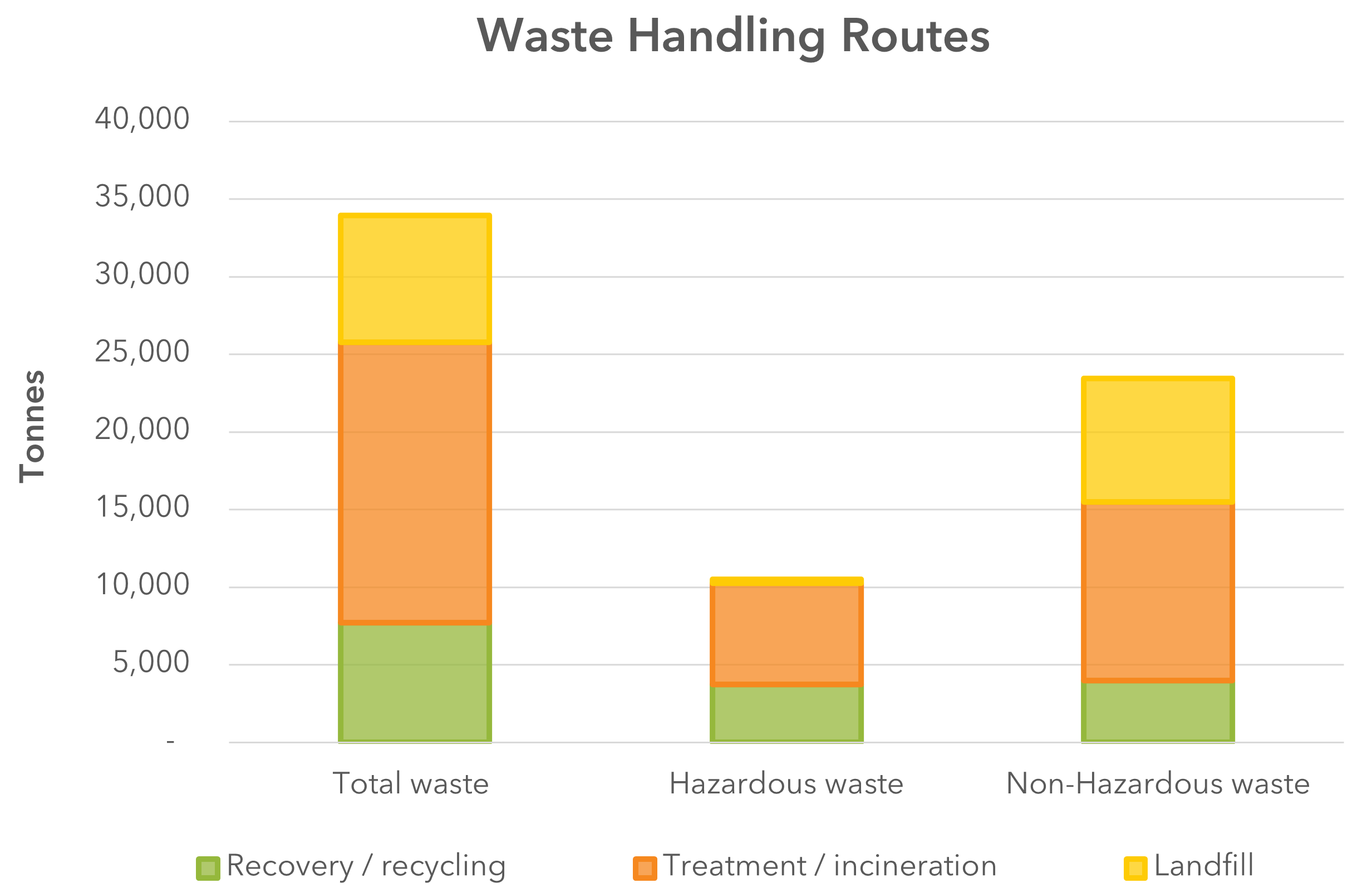
Reducing Our Waste
Barcelona, Spain
The site has adapted their process to recover and reuse a waste stream in the Enviromet Sol BA manufacturing process, saving 9 tonnes of waste per year. They also implemented the second phase of their project to optimize the use of a raw material cyclohexane. This involves the segregated collection and reuse of excess distilled material in the following batch, reducing virgin solvent usage and saving 36 tonnes of waste sent for offsite disposal each year.
Vernon, France
Following the installation of an activated carbon treatment process, the site was able to improve the quality of a process waste stream by reducing the total organic carbon content. The site has obtained permission from the regulator to discharge under licence the cleaned waste stream into Seine River avoiding off-site third-party disposal and transportation. This will save 12 tonnes of waste sent to landfill each year.
Castiglione, Italy
To reduce wastage caused by the periodic sampling of a production process and drainage of tank lines, the site has implemented a new product recovery system. The collected material is tested and then recovered into the next production batch of the product. This is avoiding 12 tonnes of product from being sent for waste treatment each year and also reduces raw material usage.
Herne, Germany
Implemented a new Olefin-Dosing Station to help better control the addition of the raw material into the process and reduce the wastage currently caused by manual dosing. The project will reduce Olefin waste by 12 tonnes per year.
Salisbury, US
The site has installed a new effluent screw press to reduce the liquid content of a waste sludge generated by the onsite wastewater treatment plant. The project has reduced the water content in the sludge by more than 70% creating a solid lighter cake that is easier to transport and handle and has saved 2,200 tonnes of waste sent for landfill each year.